提高噴油壓力需要有效且有針對性地設計噴油系統(tǒng)組件。APL公司開發(fā)了將仿真和試驗結(jié)合在一起的工具,以優(yōu)化發(fā)動機零部件在流體動壓接觸方面的摩擦損失和耐磨損性能。
1提高噴油壓力
當前和未來動力系統(tǒng)的開發(fā)重點是努力實現(xiàn)最大效率,并最大限度地減少排放。因此,不管是針對柴油機還是直噴式汽油機,提升噴油壓力是提高發(fā)動機效率并降低污染物排放(尤其是顆粒物(PM)排放)的有效方式。幾年前,乘用車用柴油機和直噴式汽油機的最大噴油壓力分別低于200 MPa和15 MPa,而如今量產(chǎn)的柴油機和直噴式汽油機的最大噴油壓力已分別達到250 MPa和35 MPa。隨著采用更貼近現(xiàn)實的全球統(tǒng)一輕型車試驗循環(huán)(WLTC)和實際行駛排放法規(guī)(RDE)循環(huán)工況等,以及滿足更嚴格的排放限值要求,柴油機和汽油機的噴油壓力將不斷提高。預計在不久的將來,柴油機和直噴式汽油機的噴油壓力將分別達到300 MPa和50 MPa。
圖1 噴油壓力對油滴大小分布和
噴霧噴射的影響
通過提高噴油壓力,可以更早達到規(guī)定的噴入燃燒室噴霧的貫穿深度和燃油質(zhì)量,如圖1(a)所示。這意味著即使在較高的發(fā)動機轉(zhuǎn)速下,噴油方式更為多樣化。這樣可有效控制燃燒過程,從而影響發(fā)動機的功率和排放。噴油壓力的提高,除了影響噴霧噴射的形狀和速度之外,還能顯著改善混合物形成和油滴大小分布(圖1(b))。當快速蒸發(fā)的表面積-體積比的小油滴增多,同時減少較大的油滴,能有效抑制碳煙生成。此外,采用索特平均直徑D32來量化噴霧質(zhì)量。在提高噴油壓力時必須避免不必要的組件接觸,以及與油膜的相互影響。
2柴油機高壓泵計算
提高噴油壓力還意味著產(chǎn)生壓力的零部件所承載的負荷增大。高壓噴油泵要承受來自燃油的較高壓力。在行程和柱塞直徑不變的情況下,柱塞端面上的最大正向力隨著所需的最大噴油壓力而線性增加。這也增大了泵內(nèi)其他部件的壓力,從而增加了摩擦接觸中的摩擦力。對此,下文將針對介質(zhì)潤滑的柴油機高壓泵(通過集成式凸輪軸和作為傳動元件的滾輪組件實現(xiàn)柱塞運動),以噴油壓力從200 MPa提高到300 MPa為例進行分析。
彈性動力軸承的表面參數(shù)取決于制造質(zhì)量,對該軸承的彈性多體系統(tǒng)進行初始計算,得出軸彎曲(由柱塞力和正時驅(qū)動負荷曲線引起)所造成的凸輪軸軸承邊緣處的混合摩擦集中區(qū)域。在實際運行中,這些邊緣在運行開始的前幾個小時就被消除,形成1個更具流體動力效果的表面。通過進一步開發(fā)參考文獻提出的基于能量的磨損預測工具,就可以根據(jù)表面參數(shù)和材料對徑向滑動軸承磨損進行基于時間和表面情況的分析。
柴油機高壓泵軸承磨損的關鍵運行區(qū)域處于轉(zhuǎn)速最低時,這時的燃油管道承受著最高壓力?;谶@一假設,計算出當轉(zhuǎn)速為3 000 r/min時的軸承運行等高線。當磨損率接近定值時,磨合完成。圖2為計算運行磨損后得到的凸輪軸軸承磨損程度等高線圖?;谧畲髩毫?00 MPa時的實際噴油壓力的點火控制曲線(MAP)圖,進一步計算生成摩擦MAP圖的轉(zhuǎn)速和負荷點工況(圖3)。
圖2 軸承A和B區(qū)域在轉(zhuǎn)速3 000 r/min時的
運行等高線圖
圖3 最大噴油壓力為200 MPa時的
摩擦MAP圖
圖4示出轉(zhuǎn)速3 000 r/min時各個摩擦接觸點的總摩擦功分布。由壓縮產(chǎn)生的活塞壓力垂直作用于滾子軸承和凸輪軸軸承。活塞導向裝置和挺柱導套承受著較小的橫向力。與滾輪相比,凸輪軸以較低的速度且相對較大的軸承間隙旋轉(zhuǎn),因此流體動力負荷能力較低。由此使得凸輪軸軸承的接觸摩擦增大。如果軸承采用聚醚醚酮等具有良好滑動和抗摩擦特性的塑料,仍可實現(xiàn)低磨損運行。所有軸承的摩擦功增大,尤其是在進一步增大凸輪軸軸承的接觸摩擦面的情況下。
圖4 提高高壓噴油泵噴油壓力后的
摩擦功分布以及減摩措施
3減摩措施
采取各種措施,從而進一步確保柴油機高壓泵的穩(wěn)定性。減小軸承間隙是提高凸輪軸軸承流體動力負荷能力的措施之一(圖4)。仿真結(jié)果表明,優(yōu)化間隙可以減少20%的接觸摩擦。然而應當注意的是,常采用塑料涂層的軸承對高溫反應非常敏感,因此軸承的潤滑劑流量應相對較多,以確保充分冷卻。為此,優(yōu)化軸承間隙時必須對這兩方面進行衡量。
仿真和試驗結(jié)果表明,將高壓泵從柴油潤滑轉(zhuǎn)換為機油潤滑,有可能降低摩擦接觸時的摩擦和磨損(圖4)。發(fā)動機機油的黏度比燃油的黏度高,因而可減少摩擦和磨損(尤其是混合摩擦區(qū)域)。此外,還可以采用減磨添加劑來優(yōu)化發(fā)動機機油,以滿足特定要求。如果采用燃油潤滑的滑動軸承沒有發(fā)生混合摩擦(如在轉(zhuǎn)速3 000 r/min時滾輪和滾輪副之間的接觸),那么采用機油潤滑時,摩擦功會隨剪切力增大而增加。
目前在乘用車領域,柴油機主要采用介質(zhì)潤滑的高壓泵來實現(xiàn)機油和燃油分離。所用的密封必須有效防止機油溢入燃油中,因為機油中的Ca、Zn等元素不利于混合物生成。因此,設計密封元件時必須保證之前取得的軸承摩擦優(yōu)勢不會因密封中的摩擦而抵消甚至會變得更差。
如噴油嘴處出現(xiàn)積炭,進而增加發(fā)動機功率損失和排放量。燃油中Ca和Zn含量與噴油器沉積物形成的關系可通過試驗證明。在此基礎上可定義機油滲入燃油的限值。開發(fā)密封概念時可采用示蹤法,并根據(jù)運行點來在線評估進入燃油系統(tǒng)的機油量。
4汽油機高壓噴射
汽油機高壓泵的介質(zhì)分離處于先進水平,這是因為汽油機的噴油壓力相對較低(最高35 MPa),并且發(fā)動機凸輪軸由采用機油潤滑的接觸來驅(qū)動。然而,隨著噴油壓力的提高,作用于凸輪軸的力和力矩也隨之增大。在汽油機高壓噴射(60 MPa)潛力評估項目中,開發(fā)了1種與常規(guī)柴油機高壓泵類似的帶獨立驅(qū)動軸的汽油機高壓泵?;趦?yōu)化摩擦損失和延長使用壽命,APL公司進行1項重大挑戰(zhàn)——研究軸承替代材料、表面輪廓和燃油潤滑的影響。
汽油機高壓泵的壓力負荷比柴油機至少小70%,且汽油黏度僅為柴油黏度的25%左右。此外,汽油(RON95)的蒸發(fā)溫度明顯更低,這使得考慮局部峰值溫度更為重要。由于汽油機轉(zhuǎn)速通常比柴油機更高,因而燃油潤滑比機油潤滑更具潛力,尤其是可以通過減小流體運動剪切力來降低摩擦功。將所引起的接觸摩擦及相應的磨損降至最低。圖5比較了機油(黏度等級為5W-30)潤滑與汽油潤滑的摩擦功分布。
圖5 潤滑介質(zhì)為機油(5W-30)與
汽油(RON95)的摩擦功分布
為了在轉(zhuǎn)速較低時仍能在有利的流體動力范圍內(nèi)使泵的凸輪軸軸承運行,首先應考慮增大軸承直徑。這樣一方面可以增加軸承的潤滑劑流量,另一方面可以降低混合摩擦比例(圖6(a))。在較高轉(zhuǎn)速和較大直徑區(qū)域的條件下,摩擦功隨著流體動力剪切力的增大而增加。通過調(diào)節(jié)軸承直徑進行的優(yōu)化受到限制。對于采用機油潤滑的軸承,增大直徑不利于降低摩擦功(圖6(b))。由于低轉(zhuǎn)速時軸承在流體動力范圍內(nèi)運行,因此,相對較高轉(zhuǎn)速的情況而言會導致剪切力較大。APL公司將進一步研究減摩替代方法,例如改變軸承寬度和通過曲軸旋轉(zhuǎn)運動的傳遞來改變轉(zhuǎn)速。
圖6 取決于軸承直徑的摩擦功
5結(jié)論與展望
提高汽油機和柴油機的噴油壓力仍是未來的發(fā)展趨勢。因此,必須進一步優(yōu)化噴油系統(tǒng)組件及其摩擦接觸,以滿足提升噴油壓力的需求。為此,APL公司采用了多種方法和設計。為了有效且有針對性地開發(fā)噴油組件,APL公司在試驗和仿真的基礎上開發(fā)了大量集成式工具鏈。并將相關的負荷譜以及不同的介質(zhì)質(zhì)量集成到現(xiàn)有的工具鏈中,APL公司致力于預測摩擦接觸的最佳表面設計,從而有助于開發(fā)出更有效的、能夠降低排放的動力系統(tǒng)。
-
噴油
+關注
關注
0文章
5瀏覽量
7220 -
柴油機
+關注
關注
1文章
170瀏覽量
26213 -
摩擦
+關注
關注
0文章
13瀏覽量
7642
發(fā)布評論請先 登錄
相關推薦
如何利用FPGA處理電控單元噴油脈寬調(diào)整問題?
基于OSEKWorks開發(fā)平臺的高壓共軌噴油控制系統(tǒng)的研究
基于典型工況的高壓共軌噴油系統(tǒng)標定
TD高負荷網(wǎng)絡性能優(yōu)化的關鍵問題
電控噴油霧化檢測的DSP和FPGA通信模塊設計

動溫度所需要的噴油脈寬l
油浸式高壓負荷開關_二工位油浸式負荷開關_四工位油浸式負荷開關
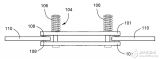
南方電網(wǎng)統(tǒng)調(diào)負荷創(chuàng)下新高,最高負荷達1.64468億千瓦
廣東省首次出現(xiàn)五年來電力供應緊張 最高負荷再增10.5%
少油斷路器常見故障及處理辦法
西北電網(wǎng)最高負荷突破1億千瓦,電力調(diào)控中心積極應對高負荷
高負荷小區(qū)的切換重選和負載均衡資料下載
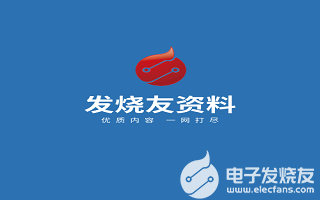
評論