作者: 張利民,王文平,范成建,馬國星
1 前言
隨著汽車電子產(chǎn)品在整車中的廣泛應(yīng)用,汽車電子產(chǎn)品的可靠性也備受關(guān)注。振動問題是影響汽車電子產(chǎn)品可靠性的一個重要因素,如果在研發(fā)設(shè)計階段就能準(zhǔn)確的預(yù)估汽車電子產(chǎn)品的振動特性,則對汽車電子產(chǎn)品的可靠性設(shè)計具有重大的意義。利用有限元技術(shù)能夠在研發(fā)設(shè)計階段預(yù)估汽車電子產(chǎn)品的振動特性,但是對于具有復(fù)雜結(jié)構(gòu)的電子產(chǎn)品來說,由于模型的復(fù)雜度,材料參數(shù)的不確定性、邊界設(shè)定的非線性、計算機配置要求等因素的影響,使仿真結(jié)果的可信度不高。因此提高仿真分析的可信度是當(dāng)今仿真工作者的首要任務(wù)。本文對某具有復(fù)雜結(jié)構(gòu)的汽車電子控制器進(jìn)行了模態(tài)仿真分析和模態(tài)試驗,并對仿真分析中的幾何模型修正,單元類型選擇,邊界條件設(shè)定等方法進(jìn)行了研究。
2 汽車電子控制器結(jié)構(gòu)介紹
汽車電子控制器由PCBA(集成電路板)和上、下殼體組成,如圖1所示(為展示控制器內(nèi)部結(jié)構(gòu),剖掉部分殼體)。裝配該控制器時,先把PCBA沿殼體上的卡槽插入下殼體中,再把上殼體扣合到下殼體上,完成裝配。該控制器在車上的安裝方式是:用螺栓穿過殼體上的安裝耳再固定到支架上。
圖1:控制器的實物圖
3 有限元建模和仿真計算
3.1 幾何模型修正
在實際工作中發(fā)現(xiàn),幾何模型修正的好壞決定著網(wǎng)格質(zhì)量的好壞。對復(fù)雜的模型來說,不修正幾何模型,會增加奇異單元的數(shù)目和單元的總數(shù)目,導(dǎo)致仿真分析周期變長,分析成本變大,甚至使仿真分析無法進(jìn)行。該控制器的PCBA上有成百上千個微小的孔和器件,殼體上有過密的硬點和線以及微小的倒圓角等,如果不修正幾何模型,在中等配置的HP工作站上無法完成分析。所以在劃分網(wǎng)格前,先對該控制器的幾何模型進(jìn)行修正。幾何模型修正工作包括:去掉較小的倒圓角和圓孔;隱藏過密的曲線和硬點;切分不規(guī)則的幾何體;忽略微小電器件等。該控制器修正后的幾何模型如圖2、圖3、圖4所示。
3.2 有限元網(wǎng)格劃分和單元類型選擇
控制器的各部件均采用3D實體單元建模。其中PCBA由電路板、電容、電阻、天線、小電路板、插件,插針等部件組成,這些部件的形狀較規(guī)則,采用一階六面體單元建模,單元類型為C3D8R,需進(jìn)行沙漏控制。上、下殼體的形狀比較復(fù)雜,用二階四面體進(jìn)行建模,單元類型為C3D10M。模態(tài)分析時,不要使用一階四面體單元,因為一階四面體單元剛性偏強,容易導(dǎo)致模態(tài)頻率偏大(下文將會給出驗證)。根據(jù)這些原則劃分的網(wǎng)格如圖5、圖6、圖7、圖8所示。
3.3 邊界條件設(shè)定
對該控制器進(jìn)行約束模態(tài)分析時,需固定安裝孔內(nèi)側(cè)面上的所有節(jié)點。上殼體的卡槽與PCBA的間隙為零或者過盈配合的部分用Tie命令進(jìn)行面對面的粘貼;下殼體的滑道和卡槽與PCBA的間隙為零或者過盈配合的部分用Tie命令進(jìn)行面對面的粘貼;PCB上的較小的電容、電阻及芯片等器件與PCB直接進(jìn)行面對面粘貼;為避免局部剛度過大對頻率和振型造成影響,把較大的電容、電阻、芯片及接插件等電器件的針腳位置的單元與PCB進(jìn)行粘貼。后文中比對了較大電器件的針腳位置的單元粘貼到PCB上的粘貼方式與面對面直接粘貼到PCB上的方式對PCBA模態(tài)頻率的影響。證實了把較大電器件的針腳位置的單元粘貼到PCB上的粘貼方式更優(yōu)越。
3.4 材料參數(shù)
該型汽車電子控制器實物的總重205.4克,其中PCBA重為100.1克,殼體重為105.3克,有限元模型總重為 204.9克,其中PCBA模型重為99.5克,殼體模型重為103.9克,實物和有限元模型重量的相對誤差為1.0%。為了簡化計算,認(rèn)為電路板具有一種等效材料參數(shù),該等效參數(shù)是通過對PCB光板的拉伸試驗和測量對其測密度得到的。同樣認(rèn)為較大的電器件也具有一種等效材料參數(shù),其彈性模量和泊松比是參考普通芯片的材料得到的,密度是由芯片的總重量除以總體積得到的。各個部件的材料參數(shù)如表1所示。
表1:各部件的材料參數(shù)
3.5 仿真分析結(jié)果
利用Abaqus軟件對該汽車電子控制器進(jìn)行約束模態(tài)分析,得到的前三階模態(tài)頻率和模態(tài)振型如圖9、圖10、圖11所示。第一階固有頻率為172Hz,第一階振型為控制器沿兩個安裝耳中心點連線的前后振動;第二階固有頻率為262Hz,第二階振型為控制器殼體上下面的相向的凸凹振動;第三階固有頻率為293Hz,第三階振型為控制器殼體上下面的相對的凸凹振動。
4 模態(tài)實驗過程及結(jié)果
4.1 模態(tài)試驗過程
利用美國PCB公司的壓電式力錘和壓電式加速度計進(jìn)行激勵、拾振。然后用LMS TEST.LAB 試驗采集分析系統(tǒng)進(jìn)行數(shù)據(jù)采集和分析。試驗設(shè)置如下,采樣頻率為2048Hz,采樣帶寬為1024Hz,頻率分辨率為0.125Hz,激勵用力窗,響應(yīng)是指數(shù)窗。
汽車電子控制器通過兩個安裝孔固定在基頻大于500Hz試驗臺上。采用了5傳感器布置方案(圖12)進(jìn)行模型試驗。參照仿真分析結(jié)果發(fā)現(xiàn),該傳感器布置方案漏掉了第一階扭轉(zhuǎn)模態(tài)。而采用8傳感器的布置方案(圖13)能測得第一階扭轉(zhuǎn)模態(tài)。
4.2 典型的實驗結(jié)果
在5傳感器的試驗中,若干點的頻率響應(yīng)函數(shù)如圖14所示。隨意選取一個測試點的相干函數(shù)如圖15所示。在有效帶寬的范圍內(nèi),相干函數(shù)接近1,可以判定頻率響應(yīng)函數(shù)的可信度比較高。在8傳感器的試驗中,若干點的頻率響應(yīng)函數(shù)如圖16所示。
利用LMS TEST.LAB軟件中的Time MDOF方法進(jìn)行模態(tài)參數(shù)分析。根據(jù)所有測試點的頻率響應(yīng)函數(shù)之和建立穩(wěn)態(tài)圖,然后判定真實的模態(tài)頻率、阻尼和參預(yù)因子。利用該方法測得的該控制器的前三階模態(tài)頻率和振型如圖17-19所示。
5 計算和試驗結(jié)果對比及分析
5.1 仿真和試驗結(jié)果對比
對比仿真分析和試驗得到的前三階振型,發(fā)現(xiàn)振型匹配很好;對比前三階頻率,發(fā)現(xiàn)最大相對誤差將近20%,如表2所示。根據(jù)以上對比結(jié)果,可以判定該試驗結(jié)果和仿真結(jié)果存在很大的誤差。為了驗證仿真分析方法是否可行,后文中將會對造成誤差的原因進(jìn)行分析。
表2:仿真結(jié)果與試驗結(jié)果的對比表
5.2 傳感器重量的影響分析
單個傳感器的重量為5克,控制器上布置多個傳感器時會引入很大的附加質(zhì)量。于是在有限元模型中添加傳感器的模型,并在考慮單元類型等因素的前提下,重新進(jìn)行模態(tài)仿真分析,算得的固有頻率和固有振型如圖20~圖22。
對比修正仿真分析和試驗得到的前三階振型,發(fā)現(xiàn)振型匹配很好;對比的前三階頻率,發(fā)現(xiàn)最大相對誤差保持在6.8%以下,如表3。根據(jù)以上分析結(jié)果,可以判定傳感器的重量是造成試驗和仿真誤差過大的主要原因。考慮傳感器影響時,仿真分析的可信度能夠達(dá)到93%以上,根據(jù)工程實際對可信度的要求,可以判定該仿真結(jié)果是控制器模態(tài)的真實反映。
表3:考慮傳感器的仿真結(jié)果與試驗結(jié)果的對比
5.3 單元類型的影響分析
本小節(jié)對一階四面體單元是否適合在模態(tài)分析中使用進(jìn)行驗證。一階四面體單元具有四個節(jié)點,邊是直線,面是平面,加載變形后邊和面仍要保持直線和平面。二階四面體單元由十個節(jié)點,邊可以是曲線,面可以是曲面,加載變形后邊和面可以是曲線和曲面。所以用一階四面體單元組成的網(wǎng)格模擬真實復(fù)雜的變形和應(yīng)力場,具有一定的局限性。使用一階四面體單元和二階四面體單元對控制器下殼體進(jìn)行約束模態(tài)分析。對比兩種情況下算得的前三階振型,發(fā)現(xiàn)振型一致;固有頻率結(jié)果如表4,對比表4中的數(shù)據(jù),發(fā)現(xiàn)用一階四面單元算得的前三階模態(tài)頻率比二階四面體單元算得的前三階模態(tài)頻率都要高,并且一階四面體單元算得的模態(tài)頻率更偏離實驗結(jié)果。所以模態(tài)仿真分析不能使用一階四面體單元。
表4:一階四面體單元和二階四面體單元對比
5.4 粘貼方式的影響分析
電器件直接面對面粘貼到PCB上的方式相比電器件針腳位置的單元粘貼到PCB上的方式會增大PCBA的局部剛性,對PCBA的自由模態(tài)有一定的影響。進(jìn)行兩種粘貼方式下的PCBA的自由模態(tài)分析,得到的模態(tài)頻率如表5。對比兩種粘貼方式下的模態(tài)頻率發(fā)現(xiàn),電器件直接面對面粘貼的方式的PCBA模態(tài)頻率偏大,證明了較大電器件直接面對面粘貼到PCB上的粘貼方式增大了PCBA的局部剛性,使得模態(tài)頻率變大。
表5:直接面面粘貼和針腳位置單元粘貼對比
6 結(jié)論
本文利用有限元軟件對某型汽車電子控制器進(jìn)行了模態(tài)仿真分析,并用模態(tài)實驗驗證了模態(tài)仿真分析結(jié)果的可信度,得到以下結(jié)論:
1、高質(zhì)量的網(wǎng)格是仿真分析順利進(jìn)行的保障,并且能縮短仿真分析周期,要得到高質(zhì)量的網(wǎng)格需去掉較小的倒圓角和圓孔,隱藏過密的曲線和硬點,切分不規(guī)則的幾何體,忽略微小的電器件等;
2、對該類控制器進(jìn)行了模態(tài)仿真分析時,不要使用一階四面體單元,否則會導(dǎo)致模態(tài)頻率偏大,可以使用一階六面體單元(對其進(jìn)行沙漏控制)和二階四面體單元。
3、對該類控制器進(jìn)行了模態(tài)仿真分析時,較大的電容、電阻、芯片及接插件等電器件不能直接面對面粘貼到PCB上,否則會增大PCBA的局部剛性,可以把較大的電容、電阻、芯片及接插件等電器件的針腳位置的單元粘貼到PCB上。
按照文中的仿真建模方法既能提高計算效率又能保障計算結(jié)果有93%以上的可信度。
責(zé)任編輯:gt
-
控制器
+關(guān)注
關(guān)注
112文章
16111瀏覽量
177083 -
汽車電子
+關(guān)注
關(guān)注
3023文章
7822瀏覽量
166017 -
仿真
+關(guān)注
關(guān)注
50文章
4023瀏覽量
133338
發(fā)布評論請先 登錄
相關(guān)推薦
汽車電子控制器的模態(tài)仿真技術(shù)研究
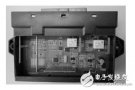
MATLAB有限元分析與應(yīng)用
深圳市有限元科技有限公司歡迎cae工程師們進(jìn)行技術(shù)交流
汽車行業(yè)的CAE解決方案-有限元科技
航空電子設(shè)備PCB組件的實驗?zāi)B(tài)分析
如何有效的學(xué)習(xí)CAE有限元分析
有限元仿真分析軟件的三種算法模型格式介紹
求一種有限元分析中PCBA的簡化建模方法
副車架靜力學(xué)分析及試驗驗證
有限元法在車身結(jié)構(gòu)反求設(shè)計中的應(yīng)用
多噴嘴引射器有限元模型修正
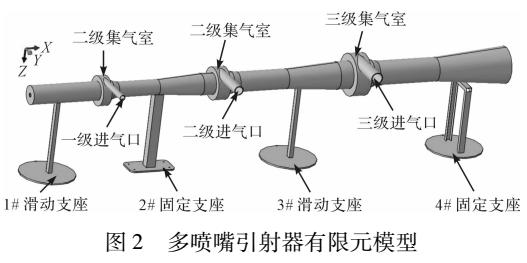
評論