目前,新能源汽車推廣主要以鋰離子電池應用為主。特斯拉電動汽車的橫空出世,以及我國一系列支持新能源汽車的政策出臺,徹底推動了我國鋰離子電池行業(yè)發(fā)展。
18650是指電池的外形規(guī)格,其中: 18表示直徑為18mm,65表示長度為65mm,0表示圓柱形電池,是最早、最成熟、最穩(wěn)定的鋰離子電池型號,其具有制造自動化水平高、電池一致性好、單體能量密度高、散熱性好等優(yōu)點。
本文作者以18650圓柱形鋰離子電池為例,揭示鋰電池制造工藝流程,分析各流程的管控要點及其對電池電性能的影響,為鋰離子電池應用提供重要的參考。
一、鋰離子電池
1. 1 鋰離子電池工作原理
鋰離子電池主要由正極、負極、隔膜和電解液組成,依靠Li+在正極和負極之間移動來工作。充電時Li+從正極脫嵌,經(jīng)過電解質(zhì)嵌入負極,負極處于富鋰狀態(tài); 放電時則相反。以鈷酸鋰為正極,石墨為負極的鋰電池為例,充電時的化學反應公式如下:
1. 2 鋰離子電池結構鋰離子電池主要由正極、負極、膈膜和電解液四大主材組成。同時,一顆完整的18650圓柱形鋰離子電芯還包括正負極引線、上下絕緣片、蓋板及外鋼殼等輔材。
二、鋰離子電池制造工藝與管控點
鋰離子電池的制造工藝復雜,工序眾多,任何一個環(huán)節(jié)出現(xiàn)失誤都將影響鋰離子電芯的性能或帶來安全問題,因此,只有嚴格管控每一道制造工序,才能制造出性能優(yōu)異和安全有保障的合格電芯。
文中以18650圓柱形鋰離子電池為例,詳細介紹電池的制造工藝并說明每一道制造工序的管控要點及其影響,并將20道制造工序分為制造前段、制造后段及篩選工藝3個階段,依次闡述。
2. 1 鋰離子電池制造前段工藝與管控點電池制造前段工藝包括合漿、涂布、輥壓、分切、制片、卷繞、入殼、底焊、輥槽及烘烤10道工序,前段工序的核心是將粉末狀的正負極材料制作成一顆卷芯。
合漿工序是指正極或負極粉末、導電劑及黏接劑按一定比例均勻混合成懸濁漿料,再將漿料通過涂布機在集流體表面涂覆一層厚度均勻的涂層,即涂布工序。涂布完成后,極片需通過輥壓機調(diào)整軋輥間隙、收放卷位置、張力等,并用試片試壓,確保試壓后的試片厚度符合工藝參數(shù)要求。
再用分切機分切成單顆電芯所需要的寬度,最后在制片機上焊接極耳并在極耳位置貼上絕緣膠包覆裸露的集流體和極耳,至此,正負極片的制作結束。
合漿工序最主要的工藝管控點在于環(huán)境的濕度控制,因為水分是鋰離子電池生產(chǎn)過程中需要嚴格控制的關鍵指標,環(huán)境濕度較大、水性黏結劑的使用等因素都會導致極片制備過程中水分含量的增加; 分切工序需重點管控極片邊緣裁切毛刺大小,且不能出現(xiàn)明顯的掉料情況,否則極片因掉料或毛刺太大而刺穿隔膜,造成短路;
制片工序應防止極耳虛焊、偏焊、漏焊或極片掉料及絕緣膠偏貼或漏貼等;
卷繞工序是圓柱形鋰電池成形的重要工藝,由條狀形正負極極片和隔膜通過卷繞機卷成圓柱形卷芯,這一工序管控要點在于負極極片必須完全包覆正極極片,而隔膜必須完全包覆負極極片,對工藝精度的要求非常高。
如果負極未充分包覆正極,則充電過程中隔膜上有析鋰現(xiàn)象發(fā)生,隨著析鋰程度加重導致正負極接觸短路,由于鋰枝晶導致的內(nèi)短路事故是電池失效的重要形式,可能引起起火爆炸等事故。如果隔膜未包覆負極,直接導致正負極接觸,電芯短路,造成嚴重安全事故。
卷芯完成后需放入鋼殼并通過底焊使得負極耳與鋼殼連接,這時整個鋼殼就是電池的負極,再通過輥槽固定鋼殼內(nèi)的卷芯。入殼與輥槽工序不能破壞卷芯,輥槽高度需嚴格把控,過低時,卷芯被破壞;
過高時,卷芯容易松動。最后將已入殼的卷芯置于烘烤箱中烘烤,直至卷芯的水分含量達到標準后才能轉入下一工序。烘烤是為了嚴控卷芯的水分含量,是至關重要的一步。
2. 2 鋰離子電池制造后段工藝與管控點
電池制造后段工藝包括注液、焊接、封口、清洗及套膜。注液即通過注液機將電解液注入烘烤后水分要求合格的卷芯,注液完成后,鋰電池的四大主材均被應用到電芯之中,注液工序關鍵在于精控注液量、控濕控溫及防水,且需達到電解液能夠較好地浸潤滲透到正負極極片的效果。
電解液量的多少直接關系著電池的安全性能和容量,如果注液量過多,電池內(nèi)部產(chǎn)氣量較大,圓柱形電池的安全閥往往會過早開啟;
如果注液量過少,電池容量會偏低而且析鋰,更容易產(chǎn)生熱失控甚至引起爆炸。再將蓋板與正極耳焊接在一起,這時整個蓋板就是電池的正極,焊接的管控點在于防止虛焊、偏焊及蓋帽外觀不良。
下一道工序就是封口,封口是將鋼殼與蓋板密封,將整個卷芯與外部環(huán)境隔離,整個卷芯就是一個密閉的電化學系統(tǒng)。封口工序是整個電芯制造最后一道至關重要的工序,其壓力成形技術的工藝穩(wěn)定性決定了電池的密封性是否完好、可靠。完成封口工序意味著一顆外形完整的電芯制造已經(jīng)全部結束。
清洗工序的目的是清除電池鋼殼表面殘留的電解液,防止電解液腐蝕鋼殼,而套膜工序是保證電芯正負極端分開,防止外部電路發(fā)生短路,同時使電池有一定的美觀度,這兩道工序還需要對外觀不良電池進行篩選。
2. 3 鋰離子電池篩選工藝與管控點
由于電池原材料、生產(chǎn)工藝等差別,電池容量、電壓、內(nèi)阻等性能存在差異,使得電池組性能達不到單體電池水平,使用壽命遠短于單體電池,影響電動汽車的使用。電池篩選工藝包括活化、化成、陳化、分選及分容工序。
活化工序即電芯套膜之后在恒溫環(huán)境擱置一段時間,使電解液充分浸潤極片和隔膜,防止因電解液浸潤不均勻而導致析鋰,活化工序需管控擱置環(huán)境溫度與擱置時間。化成工序是對鋰離子電池進行第一次充電。
這一步過程促使電極表面生成一層 “固態(tài)電解質(zhì)界面膜”(SEI膜) ,是指鋰離子電池在首次充電過程中由于電解液被氧化還原分解并沉積在電極材料表面形成的界面膜,具有離子導通、電子絕緣特性,Li+可以經(jīng)過該膜自由地嵌入和脫出。
因其固體電解質(zhì)的特征,因此被稱為 “固體電解質(zhì)界面膜”。SEI 膜是鋰離子電池能夠長期穩(wěn)定工作的保障條件,對其容量、倍率、循環(huán)、安全性能等都有至關重要的影響。
選擇合適的化成電流、化成電壓、化成溫度等,對優(yōu)化和提高電池性能有非常重要的作用,故而這一工序十分重要,實際操作過程中需防止電池反接、過充及接觸不良等。
陳化工序是將某一荷電狀態(tài)下的電芯在一定恒溫環(huán)境中擱置一段時間,通過測試前與測試后的電壓進行數(shù)據(jù)篩選,剔除壓降大或壓降異常的電芯。一般電芯內(nèi)部發(fā)生微短路或存在劇烈副反應時,電芯壓降會較大,反映出電芯性能差會有一定的安全風險。
因此,壓降是電芯篩選的重要參考指標之一。由于常溫老化用時較長,為了縮短生產(chǎn)周期,絕大多數(shù)鋰離子電池廠家采取的是高溫或高荷電態(tài)老化方式,工藝管控要點需密切監(jiān)控擱置過程中有無異常情況發(fā)生,并及時采取行動確保安全,因為一般高溫老化房是個密閉空間,初始階段不易被及時發(fā)現(xiàn),一旦發(fā)生火災,后果不堪設想。
分選工序是根據(jù)電芯交流內(nèi)阻大小分選出不同內(nèi)阻檔位電芯,剔除內(nèi)阻異常電芯,易于選取合適的電芯串聯(lián)或并聯(lián)搭配,因此,內(nèi)阻也是電芯篩選的重要參考指標之一。
分容工序即測定電芯容量后按不同容量檔位篩選電芯,剔除容量不合格電芯,由于容量與溫度關系較大,分容時的環(huán)境溫度控制越精準,容量越接近真實值,檔位分配更準確,因此,溫度控制是分容的管控要點。出貨電芯必須是經(jīng)過壓降、內(nèi)阻及容量篩選且合格的電芯。
三、寫在最后一輛純電動汽車需由上千顆18650圓柱形鋰離子電池經(jīng)串并聯(lián)方式組裝而成,其中任一顆電芯出現(xiàn)問題都有可能影響整體性能,造成 “差之毫厘,謬以千里”的局面。因此,了解鋰離子電池制造工藝流程及其管控要點,對理解因電芯差異化帶來的影響及電芯實際應用有重要的借鑒與參考意義。
來源:《純電動汽車用鋰離子電池的制造工藝與管控點》作者:宋玉潔,史瑞祥,謝鑫,陶思成
編輯:jq
-
鋰離子電池
+關注
關注
85文章
3205瀏覽量
77479 -
新能源汽車
+關注
關注
141文章
10344瀏覽量
99152 -
焊接
+關注
關注
38文章
3027瀏覽量
59522 -
電解質(zhì)
+關注
關注
6文章
803瀏覽量
19996 -
電解液
+關注
關注
10文章
835瀏覽量
23046
原文標題:鋰離子電池制造工藝與管控點解析(以18650為例)
文章出處:【微信號:Recycle-Li-Battery,微信公眾號:鋰電聯(lián)盟會長】歡迎添加關注!文章轉載請注明出處。
發(fā)布評論請先 登錄
相關推薦
通信電源系統(tǒng)的守護者:鋰離子電池
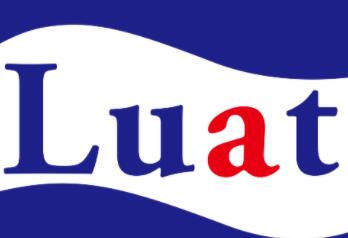
鋰離子電池化成及分容工藝概述
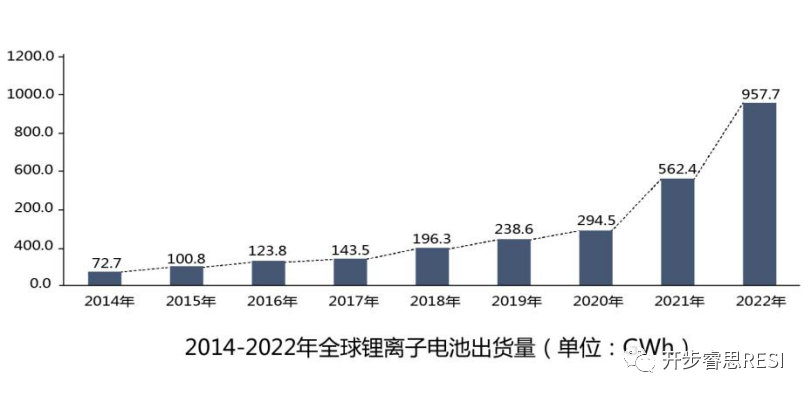
評論