電路板被很多人譽為電子產(chǎn)品之母,它是計算機、手機等消費電子產(chǎn)品的關(guān)鍵部件,在醫(yī)療、航空、新能源、汽車等行業(yè)有著廣泛應(yīng)用??v觀全球技術(shù)發(fā)展簡史,每一次技術(shù)進步都直接或間接影響著全人類。在電路板誕生之前,電子設(shè)備都包含許多電線,它們不僅會糾纏在一起,占用大量空間,而且短路的情況也不罕見。這個問題對于電路相關(guān)的工作人員來說是個非常頭疼的問題。1925年,來自美國的Charles Ducas提出了一個前所未有的想法,即在絕緣基板上印刷電路圖案,隨后進行電鍍以制造用于布線的導(dǎo)體,專業(yè)術(shù)語“PCB”由此而來,這種方法使制造電器電路變得更為簡單。
當(dāng)今世界科技飛速發(fā)展促進電子器件向集成化、微型化、高功率密度的方向發(fā)展,因此給電子器件散熱帶來了嚴(yán)峻的挑戰(zhàn)。良好散熱效果依賴于優(yōu)異的散熱結(jié)構(gòu)設(shè)計、熱界面材料、散熱基板、封裝制造工藝等。基板作為承載集成電路芯片的載體,與電路直接接觸,電路產(chǎn)生的熱量需要通過基板向外疏散。選擇一種兼具高熱導(dǎo)率與良好電絕緣性的基板材料成為解決當(dāng)下電子器件散熱問題的關(guān)鍵。
由于傳統(tǒng)覆銅板由于低的熱導(dǎo)率以及具有導(dǎo)電性限制了在當(dāng)今高功率器件中的應(yīng)用。因此開發(fā)出具有高熱導(dǎo)率和良好的電氣互連的基板材料成為了當(dāng)下的研究重點方向。目前市面上的PCB從材料大類上來分主要可以分為三種:普通基板、金屬基板、陶瓷基板。傳統(tǒng)的普通基板和金屬基板不能滿足當(dāng)下工作環(huán)境下的應(yīng)用。陶瓷基板具有絕緣性能好、強度高、熱膨脹系數(shù)小、優(yōu)異的化學(xué)穩(wěn)定性和導(dǎo)熱性能脫穎而出,是符合當(dāng)下高功率器件設(shè)備所需的性能要求。
01
介紹
陶瓷基板制備工藝流程多、流程復(fù)雜繁瑣,一款導(dǎo)熱性能優(yōu)異的陶瓷基板離不開性能優(yōu)異的粉體、精細(xì)的制備技術(shù)和嚴(yán)苛的測試。
1.1 陶瓷粉體
目前常用的高導(dǎo)熱陶瓷粉體原料有氧化鋁(Al2O3)、氮化鋁(AlN)、氮化硅(Si3N4)、碳化硅(SiC)和氧化鈹(BeO)等。隨著國家大力發(fā)展綠色環(huán)保方向,由于氧化鈹有毒性逐漸開始退出歷史的舞臺。碳化硅又因為其絕緣性差,無法應(yīng)用在微電子電路中。而Al2O3、AlN、Si3N4陶瓷粉體具有無毒、高溫穩(wěn)定性好、導(dǎo)熱性好,以及與Si、SiC和GaAs等半導(dǎo)體材料相匹配的熱膨脹系數(shù),得到了廣泛推廣應(yīng)用。幾種粉體的熱導(dǎo)率和綜合評價如下表所示,目前主流用于制備陶瓷基板的粉體原料還是以氧化鋁和氮化鋁為主。
來源:熱管理材料整理
市場中粉體的制備方法主要有硅粉直接氮化法、自蔓延高溫合成法、碳熱還原法。
(1)硅粉直接氮化法和自蔓延高溫合成法是比較主流的方法,但由于反應(yīng)溫度接近甚至超過原料的熔點,往往造成產(chǎn)物形貌不規(guī)則、ɑ相含量低、團聚嚴(yán)重,需要進一步破碎,在后續(xù)處理中容易引入其他雜質(zhì);
(2)碳熱還原法是具有原料豐富、工藝簡單、成本低等優(yōu)點,非常適合大批量生產(chǎn);其中碳熱還原法成為目前最常用的粉體制備技術(shù)之一。
1.2陶瓷基板制備工藝
流延成型技術(shù)是標(biāo)準(zhǔn)的濕法成型工藝,可一次性成型制備厚度范圍在幾十微米到毫米級別的陶瓷生坯,并通過進一步的層壓、脫脂、燒結(jié)形成陶瓷基片,主要應(yīng)用于電子基板、多層電容器、多層封裝、壓電陶瓷等。與傳統(tǒng)的粉末冶金干法制備工藝相比,流延工藝制備出的陶瓷薄片均勻性好、通透性高,在要求比較高的集成電路 領(lǐng)域深受歡迎。陶瓷基板常用的成型方法主要以流延成型為主。流延工藝的流程圖如下所示:來源:陶瓷材料流延成型工藝的研究進展
流延漿料是流延成型的重要組成部分,根據(jù)溶劑性質(zhì)的不同,流延漿料又分為有機流延成型工藝和水基流延成型工藝。(1)陶瓷粉體是流延漿料的主相,是坯片的主要成分, 影響著流延成品的導(dǎo)熱性、電阻率、介電常數(shù)、化學(xué)穩(wěn)定 性以及機械強度。陶瓷粉體的顆粒尺寸、粒度分布以及粉體的結(jié)晶形貌都對流延工藝以及流延膜的質(zhì)量有較大影響, 因此在選擇粉體的時候需要考慮以下特征:化學(xué)純度、顆粒尺寸、粉體形貌;(2)粘結(jié)劑作為流延漿料體系的唯一連續(xù)相,它能包裹住粉料顆粒,并固化形成三維立體結(jié)構(gòu),增加流延膜的強度。粘結(jié)劑和增塑劑共同作用可以提高生坯片的強 度,并改善韌性與延展性,便于生坯片與載體膜的脫離以及后續(xù)加工;(3)粉體顆粒在漿料中的分散性和均勻性與流延膜的 品質(zhì)息息相關(guān)。解決粉體團聚的主要方式有物理分散與化學(xué)分散,而在漿料中加入分散劑是流延技術(shù)中最常用的手段;(4)除上述成分外,流延漿料還會加入一些功能性添加 劑來改善流延膜制備過程產(chǎn)生的缺陷,如消泡劑、潤滑 劑、均質(zhì)劑、絮凝劑、控流劑等;
1.4陶瓷燒結(jié)燒結(jié)是利用熱能使粉末坯體致密化的技術(shù),其具體的定義是指多孔狀態(tài)的坯體在高溫條件下,表面積減小,孔隙率降低,力學(xué)性能(機械強度等)提高的致密化過程。坯體在燒結(jié)過程中要發(fā)生一系列的物理化變化,如膨脹,收縮,氣體的產(chǎn)生,液相的出現(xiàn),舊晶相的消失,新晶相的形成等。在不同的溫度,氣氛條件下,所發(fā)生變化的內(nèi)容與程度也不相同,從而形成不同的晶相組成和顯微結(jié)構(gòu),決定了陶瓷制品不同的質(zhì)量和性能。
燒結(jié)可分為有液相參加的燒結(jié)和純固相燒結(jié)兩類。燒結(jié)過程對陶瓷生產(chǎn)具有很重要的意義。為降低燒結(jié)溫度,擴大燒成范圍,通常加入一些添加物作助熔劑,形成少量液相,促進燒結(jié)。陶瓷燒結(jié)是陶瓷加工中的一種重要工藝,其過程分為三個階段:預(yù)燒階段、燒結(jié)階段和冷卻階段。
預(yù)燒階段:在這個階段,陶瓷制品會被放入爐子中進行預(yù)燒處理,用來去除陶瓷中的水分和有機物質(zhì)。高溫下,水分和有機物質(zhì)會被分解并釋放出來,讓制品干燥且有機物質(zhì)燃燒殆盡。這一階段的主要目的是為了減少燒結(jié)時產(chǎn)生的氣泡等缺陷。
燒結(jié)階段:在預(yù)燒之后,制品會被加熱到高溫下進行燒結(jié)。這個階段是陶瓷工藝中最關(guān)鍵的一步,也是最困難的一步。在高溫下,陶瓷顆粒會開始熔化和結(jié)合在一起,形成一個堅固的陶瓷結(jié)構(gòu)。這一階段需要控制好溫度、時間和壓力等因素,使得陶瓷能夠充分結(jié)合,而不會出現(xiàn)燒結(jié)不完全或者表面開裂等缺陷。
冷卻階段:在燒結(jié)完成后,制品需要進行冷卻,使得陶瓷結(jié)構(gòu)能夠逐漸穩(wěn)定下來。如果制品過早地被取出爐子,容易導(dǎo)致熱應(yīng)力而產(chǎn)生裂紋。因此,一般會采取緩慢冷卻的方式,讓制品溫度逐漸降下來。在冷卻過程中,還需要將爐門緩慢地打開,逐漸將爐內(nèi)壓力和爐外壓力平衡,以避免制品瞬間受到外界壓力而發(fā)生破裂。
1.5 陶瓷材料的導(dǎo)熱性影響因素
高導(dǎo)熱性非金屬固體通常具備以下4個條件:構(gòu)成的原子要輕、原子間的結(jié)合力要強、晶格結(jié)構(gòu)要單純、晶格振動的對稱性要高。陶瓷材料的導(dǎo)熱性的影響因素:(1)原料粉體,原料粉體的純度、粒度、物相會對材料的熱導(dǎo)率、力學(xué)性能產(chǎn)生重要影響。由于非金屬的傳熱機制為聲子傳熱,當(dāng)晶格完整無缺陷時,聲子的平均自由程越大,熱導(dǎo)率越高,而晶格中的氧往往伴隨著空位、位錯等結(jié)構(gòu)缺陷,顯著地降低了聲子的平均自由程,導(dǎo)致熱導(dǎo)率降低;
(2)在燒結(jié)過程,添加的燒結(jié)助劑中可以與陶瓷粉體表面的原生氧化物發(fā)生反應(yīng),形成低熔點的共晶熔液,利用液相燒結(jié)機理實現(xiàn)致密化。然而,燒結(jié)助劑所形成的晶界相自身的熱導(dǎo)率較低,對陶瓷熱導(dǎo)率具有不利影響,特別地,如氮化硅陶瓷常用的Al2O3燒結(jié)助劑,在高溫下會與氮化硅和其表面氧化物形成SiAlON固溶體,造成晶界附近的晶格發(fā)生畸變,對聲子傳熱產(chǎn)生阻礙,從而大幅度降低氮化硅陶瓷的熱導(dǎo)率。因此選用適合的燒結(jié)助劑,制定合理的配方體系是提升氮化硅熱導(dǎo)率的關(guān)鍵途徑.
02
陶瓷基板金屬化
目前導(dǎo)熱的陶瓷基板可分為HTCC(高溫共燒多層陶瓷)、LTCC(低溫共燒陶瓷)、DBC(直接鍵合銅陶瓷基板)和DPC(直接鍍銅陶瓷基板)、活性金屬纖焊陶瓷基板(AMB)等幾種形式,其特點如下。
來源:熱管理材料整理
對于大功率器件而言,基板除具備基本的機械支撐與電互連功能外,還要求具有高的導(dǎo)熱性能。因為HTCC/LTCC的熱導(dǎo)率較低,因此在高功率的器件以及IGBT模組的使用場景中散熱基板目前主要以DBC、DPC、AMB三種金屬化技術(shù)為主。
2.1DPC技術(shù)
DPC技術(shù)是先其制作首先將陶瓷基片進行前處理清洗,利用真空濺射方式在基片表面沉積 Ti/Cu 層作為種子層,接著以光刻、顯影、刻蝕工藝完成線路制作,最后再以電鍍/化學(xué)鍍方式增加線路厚度,待光刻膠去除后完成基板制作。關(guān)鍵技術(shù)涉及激光打技術(shù)、避免孔壁熔渣、鍍銅的一致性、填孔效果等。
來源:AIN應(yīng)用性能出眾,國產(chǎn)替代機遇顯著
DPC 技術(shù)具有如下優(yōu)點:(1)低溫工藝(300 ℃以下),完全避免了高溫對材料或線路結(jié)構(gòu)的不利影響,也降低了制造工藝成本;(2)采用薄膜與光刻顯影技術(shù),使基板上的金屬線路更加精細(xì)(線寬尺寸 20~30 m,表面平整度低于0.3 m,線路對準(zhǔn)精度誤差小于±1%),因此 DPC 基板非常適合對準(zhǔn)精度要求較高的電子器件封裝。
2.2DBC技術(shù)
DBC是陶瓷基片與銅箔在高溫下(1065℃)共晶燒結(jié)而成,最后根據(jù)布線要求,以刻蝕方式形成線路。由于銅箔具有良好的導(dǎo)電、導(dǎo)熱能力,而氧化鋁能有效控制 Cu-Al2O3- Cu 復(fù)合體的膨脹,使 DBC 基板具有近似氧化鋁的熱膨脹系數(shù)。關(guān)鍵技術(shù)涉及鍵合工藝、如何減少孔隙、翹曲的控制、精確控溫、氧化層的控制等。
來源:AIN應(yīng)用性能出眾,國產(chǎn)替代機遇顯著
DBC 具有導(dǎo)熱性好、 絕緣性強、可靠性高等優(yōu)點,已廣泛應(yīng)用于 IGBT、LD 和 CPV 封裝。DBC 缺點在于, 其利用了高溫下 Cu 與Al2O3間的共晶反應(yīng),對設(shè)備和工藝控制要求較高,基板成本較高;由于Al2O3與 Cu 層間容易產(chǎn)生微氣孔,降低了產(chǎn)品抗熱沖擊性;由于銅箔在高溫下容易翹曲變形。
2.3AMB技術(shù)
AMB 技術(shù)是指,在 800℃左右的高溫下,含有活性元素 Ti、Zr 的 AgCu 焊料在陶瓷和金屬的界面潤濕并反應(yīng),從而實現(xiàn)陶瓷與金屬異質(zhì)鍵合的一種工藝技術(shù)。AMB陶瓷基板,首先通過絲網(wǎng)印刷法在陶瓷板材的表面涂覆上活性金屬焊料,再與無氧銅層裝夾,在真空釬焊爐中進行高溫焊接,然后刻蝕出圖形制作電路,最后再對表面圖形進行化學(xué)鍍。關(guān)鍵技術(shù)涉及如何控制Ti的氧化和偏析、高溫下有機物的揮發(fā)導(dǎo)致孔洞和界面不致密的問題。來源:《熱管理材料》整理
AMB工藝是金屬釬料實現(xiàn)氮化鋁與無氧銅的高溫結(jié)合,以結(jié)合強度高、冷熱循環(huán)可靠性好等優(yōu)點,不僅具有更高的熱導(dǎo)率、更好的銅層結(jié)合力,而且還有熱阻更小、可靠性更高等優(yōu)勢。AMB陶瓷基板缺點在于工藝的可靠性很大程度上取決于活性釬料成分、焊工藝、舒焊層組織結(jié)構(gòu)等諸多關(guān)鍵因素,工藝難度大,而且還要兼顧成本方面的考慮。
03
應(yīng)用領(lǐng)域
3.1高鐵、新能源汽車、風(fēng)力、5G基站用IGBT模塊
由于 IGBT輸出功率高,發(fā)熱量大,散熱不良將損壞 IGBT 芯片,因此對 IGBT封裝而言,散熱是關(guān)鍵,必須選用陶瓷基板強化散熱。氮化鋁、氮化硅陶瓷基板具有熱導(dǎo)率高、與硅匹配的熱膨脹系數(shù)、高電絕緣等優(yōu)點,非常適用于 IGBT 以及功率模塊的封裝。廣泛應(yīng)用于軌道交通、航天航空、電動汽車、風(fēng)力、太陽能發(fā)電等領(lǐng)域。
3.2 LED封裝
縱觀LED技術(shù)發(fā)展,功率密度不斷提高,對散熱的要求也越來越高。由于陶瓷具有的高絕緣、高導(dǎo)熱和耐熱、低膨脹等特性,特別是采用通孔互聯(lián)技術(shù),可有效滿足LED倒裝、共晶、COB(板上芯片)、CSP(芯片規(guī)模封裝)、WLP (圓片封裝)封裝需求,適合中高功率LED封裝。
來源:百度
3.3光伏/芯片模組
光伏發(fā)電是根據(jù)光生伏特效應(yīng)原理,利用太陽能電池將太陽光直接轉(zhuǎn)化為電能。由于聚焦作用導(dǎo)致太陽光密度增加,芯片溫度升高,必須采用陶瓷基板強化散熱。實際應(yīng)用中,陶瓷基板表面的金屬層通過熱界面材料(TIM)分別與芯片和熱沉連接,熱量通過陶瓷基板快速傳導(dǎo)到金屬熱沉上,有效提高了系統(tǒng)光電轉(zhuǎn)換效率與可靠性。
04
行業(yè)分析
陶瓷基板具備散熱性好、耐熱性好、熱膨脹系數(shù)與芯片材料匹配、絕緣性好等優(yōu)點,被廣泛用于大功率電子模塊、航空航天、軍工電子等產(chǎn)品。高功率IGBT、SiC 功率器件搭載上車,刺激上游陶瓷基板的需求,推動產(chǎn)業(yè)發(fā)展,近期多個公司宣布陶瓷基板項目的投產(chǎn)或擴建計劃。
5.1全球陶瓷基板市場火爆,市場規(guī)模穩(wěn)步增加
根據(jù)華西證劵研究所報告顯示,2020 年全球陶瓷基板市場規(guī)模達到 89 億美元,預(yù)計 2026 年全球規(guī)模將達到 172.9 億美元,漲幅達到 94.27%,市場前景廣闊。
來源:《熱管理材料》整理
5.2 高功率IGBT模塊持續(xù)推動DBC/AMB陶瓷基板市場擴大
DBC 陶瓷基板具有高強度、 導(dǎo)熱性能強以及結(jié)合穩(wěn)定的優(yōu)質(zhì)性能,而AMB 陶瓷基板是在 DBC 的基礎(chǔ)上發(fā)展而來的,結(jié)合強度相對更高。近年來隨著新能源汽車、光伏儲能行業(yè)的快速發(fā)展, IGBT 功率模塊的需求快速增長,對于 DBC、 AMB 陶瓷基板的需求也不斷增加。目前 DBC 陶瓷基板主要生產(chǎn)廠家有羅杰斯、賀利氏集團、高麗化工等;AMB 陶瓷基板主要生產(chǎn)廠家有羅杰斯、日本京瓷、日本丸和等。
5.3LED需求量提高
LED 芯片對于散熱要求極為苛刻,車載照明將進一步提升 AlN 基板的需求。目前單芯片 1W 大功率 LED 已產(chǎn)業(yè)化, 3W、 5W,甚至 10W 的單芯片大功率 LED 也已推出,并部分走向市場。這使得超高亮度 LED 的應(yīng)用面不斷擴大,從特種照明的市場領(lǐng)域逐步走向普通照明市場。由于 LED 芯片輸入功率的不斷提高,對這些功率型 LED 的封裝技術(shù)提出了更高的要求。而傳統(tǒng)的基板無法承載高功率的熱能,氮化鋁陶瓷具有良好的導(dǎo)熱和絕緣性能,能夠提高 LED 功率水平和發(fā)光效率。功率 LED 已經(jīng)在戶外大型看板、小型顯示器背光源、車載照明、室內(nèi)及特殊照明等方面獲得了大量應(yīng)用。DPC 陶瓷基板憑借其電路精度高且制備溫度低的特點,被廣泛用于高精度、小體積封裝產(chǎn)品中,在高功率發(fā)光二極管中被廣泛使用。數(shù)據(jù)顯示,2020 年 DPC 陶瓷基板全球市場規(guī)模達到 12 億美元,預(yù)計 2026 年達到 17 億美元。
-
電路板
+關(guān)注
關(guān)注
140文章
4877瀏覽量
97207 -
大功率器件
+關(guān)注
關(guān)注
0文章
15瀏覽量
6714 -
陶瓷基板
+關(guān)注
關(guān)注
5文章
205瀏覽量
11398
發(fā)布評論請先 登錄
相關(guān)推薦
高功率器件設(shè)備散熱用陶瓷基板 | 晟鵬耐高溫高導(dǎo)熱絕緣片
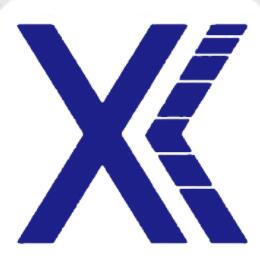
TAS5805M做最大功率2*23W時,需要加散熱片嗎?
大功率晶閘管模塊的熱管理與散熱解決方案
高導(dǎo)熱陶瓷基板,提升性能必備
大功率器件散熱裝置設(shè)計探討
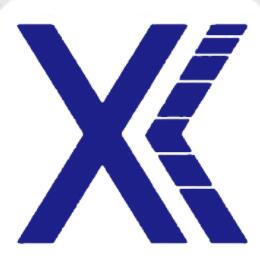
電子設(shè)備散熱,捷多邦用DPC陶瓷基板說“我行”
UPS大功率電源有何優(yōu)勢?購買大功率UPS電源的訣竅
什么是大功率繞線電阻?大功率繞線電阻器的優(yōu)點
什么是DPC陶瓷基板?DPC陶瓷基板有哪些特點?
導(dǎo)電固晶膠在大功率 LED 熱電制冷的應(yīng)用
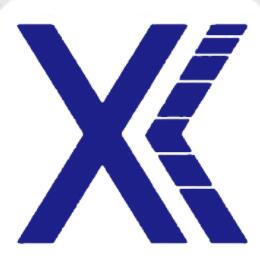
評論