傳統(tǒng)的封裝技術(shù)已難以滿足飛速發(fā)展的電子信息系統(tǒng)的高密度集成需求,隨著先進(jìn)封裝技術(shù)的發(fā)展,射頻微系統(tǒng)成為小型化電子產(chǎn)品的重要組成部分,可以在微納尺度下實現(xiàn)高性能電子系統(tǒng),為電子信息設(shè)備多方面的技術(shù)變革提供了重要技術(shù)路徑[1],典型射頻微系統(tǒng)如圖1所示。自射頻微系統(tǒng)技術(shù)問世以來,美國、日本等發(fā)達(dá)國家就將其列為現(xiàn)代前沿核心技術(shù),并相繼實施了“超越微縮(Beyond Scaling)”、“電子復(fù)興ERI計劃(Electronic Renaissance Initiative)”、“E-CUBES計劃”等項目計劃。另外,臺積電、Intel、IBM等公司也紛紛對射頻微系統(tǒng)的新技術(shù)、新工藝展開研究并取得不菲成果。掌握射頻微系統(tǒng)技術(shù)對于國家實現(xiàn)核心技術(shù)自主可控具有重要意義,因此,我國近年來對射頻微系統(tǒng)技術(shù)高度重視并進(jìn)行深入研究[2],先后大力支持了遙感信息處理微系統(tǒng)集成、彈載多模通信等方向的課題研究工作。
本文首先對射頻微系統(tǒng)的發(fā)展與應(yīng)用進(jìn)行分析,接著梳理總結(jié)了射頻微系統(tǒng)幾種典型技術(shù)的內(nèi)涵及研究現(xiàn)狀,最后針對國內(nèi)射頻微系統(tǒng)的發(fā)展現(xiàn)狀,探討了現(xiàn)階段主要存在的問題,并對射頻微系統(tǒng)未來發(fā)展策略提出了一些建議。
1 射頻微系統(tǒng)技術(shù)概述
摩爾定律已經(jīng)逼近極限,目前集成電路主要沿三個方向發(fā)展:延續(xù)摩爾定律(More Moore)、拓展摩爾定律(Morethan Moore)以及超越CMOS(Beyond CMOS)。而射頻微系統(tǒng)技術(shù)融合了三維異質(zhì)異構(gòu)集成、微納工藝等技術(shù),可將延續(xù)摩爾定律和拓展摩爾定律的技術(shù)優(yōu)勢結(jié)合起來,實現(xiàn)高性能、多功能、小尺寸、低成本的電子封裝。射頻微系統(tǒng)的實現(xiàn)與發(fā)展途徑如圖2所示。
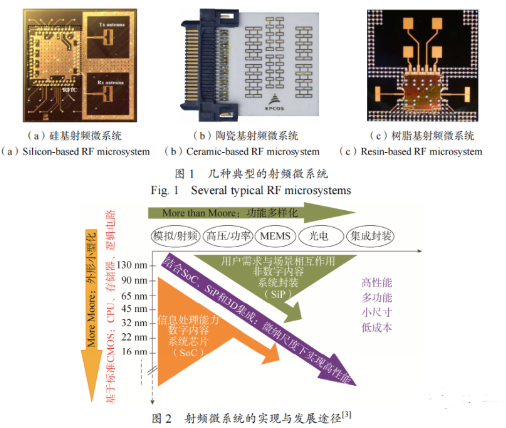
1.1 射頻微系統(tǒng)技術(shù)在軍民領(lǐng)域的應(yīng)用
射頻微系統(tǒng)主要針對雷達(dá)、通信、電子對抗、物聯(lián)網(wǎng)等產(chǎn)品的低成本、小型化、多功能化等需求,在航空航天、船舶、武器等軍事領(lǐng)域,以及5G移動通信、WiFi、生物醫(yī)療、工業(yè)控制、汽車電子等民用領(lǐng)域都有著巨大的生命力。
在軍事領(lǐng)域,射頻微系統(tǒng)作為支撐航天工程和武器裝備戰(zhàn)略發(fā)展的核心技術(shù)之一,能夠在大幅減小武器系統(tǒng)的體積與功耗的同時兼顧多功能集成和智能化,從而增強(qiáng)武器裝備在作戰(zhàn)時的機(jī)動性、可靠性和隱蔽性[4]。美國、德國、日本等發(fā)達(dá)國家已取得較多成果,研制出了采用射頻微系統(tǒng)技術(shù)的新一代雷達(dá)、通信、電子戰(zhàn)等先進(jìn)武器裝備。2013年,美國NASA成功發(fā)射的4顆采用微系統(tǒng)技術(shù)開發(fā)的手機(jī)衛(wèi)星尺寸與馬克杯大小相當(dāng),可以滿足多種系統(tǒng)需求[5]。2015年9月,日本電報與電話公司(NTT)、富士通和美國NIST研究所采用微納制造工藝,將聚酰亞胺作為印制電路板,結(jié)合太赫茲高靈敏放大器芯片集成技術(shù),合作研發(fā)出世界首個內(nèi)置天線的緊湊型300GHz接收器,體積僅為0.75cm3。2016年4月,德國Fraunhofer研究所采用InGaAs器件技術(shù)和特制印刷電路板研發(fā)出了一款高頻微系統(tǒng)模塊,體積僅為78mm×42mm×28mm,可使雷達(dá)模塊體積縮減至煙盒大小。2018年,美國DARPA與佐治亞理工學(xué)院等機(jī)構(gòu)合作啟動了三維單芯片系統(tǒng)3DSoC(3DSystemonChip)項目,實現(xiàn)了存儲、邏輯和收發(fā)組件等單元小型化、一體化、高性能三維射頻微系統(tǒng)封裝芯片,并于2020年6月的“2020 VLSI技術(shù)與電路研討會”上首次對單片集成3D SoC技術(shù)與SRAM和RISC-V計算核進(jìn)行了硬件演示,并宣稱已為3D SoC技術(shù)平臺開發(fā)了工業(yè)級代工工藝設(shè)計套件PDK(Process Design Kit)。
在民用領(lǐng)域,射頻微系統(tǒng)已經(jīng)廣泛應(yīng)用于短距離無線通信、物聯(lián)網(wǎng)、5G通信、智能駕駛等領(lǐng)域。通過TSV技術(shù)、晶圓鍵合技術(shù)等先進(jìn)射頻微加工技術(shù),可以大大提高微波收發(fā)組件、數(shù)據(jù)處理器件、高頻存儲器件、高效電源等的集成度,優(yōu)化產(chǎn)品性能。2015年,英特爾公司[6]通過將收發(fā)組件集成于包含天線元件的液晶聚合物L(fēng)CP(Liquid Crystal Polymer)封裝中,實現(xiàn)了一款集成了18個收發(fā)組件的60GHz相控陣射頻微系統(tǒng),主要用于60GHzWiGig領(lǐng)域,封裝薄至0.41mm。2017年,IBM公司為毫米波5G通信系統(tǒng)開發(fā)了一款基于高密度互連HDI(High Density Interconnector)工藝的Ka頻段16通道相控陣射頻微系統(tǒng)[7],尺寸僅為6.85mm×6.85mm×1.61mm。2020年,新加坡A*STAR研究所針對5G應(yīng)用設(shè)計了一款封裝尺寸為10mm×10mm×0.8mm的雙層模壓扇出式晶圓級封裝FOWLP(Fan-out Wafer Level Packaging)射頻微系統(tǒng)[8],散熱能力高達(dá)5W。2020年,大陸集團(tuán)宣布,通過賽靈思公司的Zynq?UltraScale+?MPSoC平臺,開發(fā)出了新型高分辨率遠(yuǎn)程4D成像雷達(dá)傳感器ARS540,可在智能駕駛中實現(xiàn)復(fù)雜駕駛場景的多目標(biāo)跟蹤、快速識別相應(yīng)道路潛在的危險物體等功能。
1.2 射頻微系統(tǒng)典型技術(shù)
射頻微系統(tǒng)典型技術(shù)主要包括射頻微系統(tǒng)設(shè)計與仿真、射頻微系統(tǒng)三維集成技術(shù)、熱管理技術(shù)以及檢測和測試驗證技術(shù)。射頻微系統(tǒng)技術(shù)體系架構(gòu)細(xì)分圖如圖3所示。
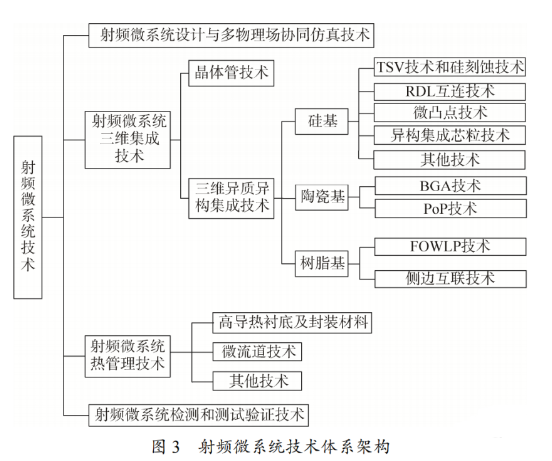
2 射頻微系統(tǒng)設(shè)計與多物理場協(xié)同仿真技術(shù)
射頻微系統(tǒng)設(shè)計主要是根據(jù)微系統(tǒng)的應(yīng)用需求對各功能模塊進(jìn)行合理設(shè)計及布局,以實現(xiàn)三維射頻微系統(tǒng)封裝中電路信號的完整性要求,避免信號串?dāng)_問題和垂直互連結(jié)構(gòu)信號過渡不連續(xù)問題。
在射頻微系統(tǒng)技術(shù)實現(xiàn)的產(chǎn)品工作過程中,電、磁、熱、力等物理場并不是單獨存在和作用的,各物理場間往往會相互耦合、相互影響[9],因此,在射頻微系統(tǒng)封裝的設(shè)計中需要進(jìn)行多物理場協(xié)同仿真研究。通過對射頻微系統(tǒng)中光、機(jī)、電、磁、熱、流體、應(yīng)力應(yīng)變等多維度物理場在微小尺度下的耦合與互擾進(jìn)行研究,以解決多元參量間相互約束和平衡問題,進(jìn)而采用一些特殊的設(shè)計來提高射頻多芯片的電氣性能,并減少多物理場對產(chǎn)品可靠性的影響。2016年,美國伊利諾伊大學(xué)香檳分校針對集成微流道冷卻的三維射頻微系統(tǒng),提出了一種包括全波電磁、流體、瞬態(tài)共軛熱交換的多物理場協(xié)同仿真技術(shù)[10],其通過對流體流動的控制方程與溫度解耦解析出流體的速度場,全波電磁和瞬態(tài)共軛傳熱分析通過溫控材料來進(jìn)行耦合迭代分析,實現(xiàn)了精確、高效的多物理場協(xié)同仿真,并驗證了微流道散熱的有效性以及對3D射頻微系統(tǒng)高頻特性的熱影響。
3 射頻微系統(tǒng)三維集成技術(shù)
結(jié)合延續(xù)摩爾定律與拓展摩爾定律的射頻微系統(tǒng)三維集成技術(shù),可以分為晶體管技術(shù)、高密度封裝功能基板制造技術(shù)、三維異質(zhì)異構(gòu)集成技術(shù)。其中,晶體管技術(shù)主要在延續(xù)摩爾定律方面進(jìn)行技術(shù)研究和突破,以獲得按比例微縮的高性能芯片;三維異質(zhì)異構(gòu)集成技術(shù)主要用于拓展摩爾定律,通過先進(jìn)封裝技術(shù),在成本相對低廉的情況下實現(xiàn)系統(tǒng)小型化、多功能和高性能。
3.1 晶體管技術(shù)
隨著摩爾定律的發(fā)展,傳統(tǒng)平面MOSFET結(jié)構(gòu)的限制使得半導(dǎo)體工藝逐漸難以滿足“等比例微縮”的尺寸發(fā)展需求。為繼續(xù)向微型化發(fā)展,一種新結(jié)構(gòu)——三維結(jié)構(gòu)的鰭式晶體管FinFET(FinField-EffectTransistor)——應(yīng)運而生。英特爾、三星、臺積電陸續(xù)在其工藝制程節(jié)點上推出了各自的FinFET技術(shù)。FinFET技術(shù)最主要的特點是柵極(Gate)三面環(huán)繞源極(Source)和漏極(Drain)之間的溝道,由于增加了柵極對溝道的控制面積,因此能有效減小漏電流,增強(qiáng)溝道控制能力,進(jìn)一步縮短柵極長度,減小晶體管面積。
為應(yīng)對芯片采用FinFET技術(shù)微縮到7nm后的瓶頸,三星、英特爾等突破性地提出了環(huán)繞柵極場效應(yīng)晶體管GAAFET(GateAllAroundFieldEffectTransistors)技術(shù)。GAAFET技術(shù)在給定的區(qū)域內(nèi)封裝了更多的高性能晶體管,其與FinFET技術(shù)相比,減小了標(biāo)準(zhǔn)單元的寬度。GAAFET技術(shù)可以分為兩種,一是常規(guī)GAAFET,使用三層納米線(nanowire)替代FinFET的鰭;二是多橋通道場效應(yīng)晶體管MBCFET(Multi-Bridge-ChannelMOSFET),其使用更厚更寬的納米片(nanosheet)作為晶體管的鰭,增加了溝道和柵極間接觸面積,從而增大了電流通過量[11,12]。各結(jié)構(gòu)對比如圖4所示。
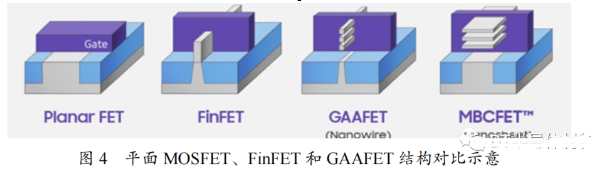
3.2 三維異質(zhì)異構(gòu)集成技術(shù)
射頻微系統(tǒng)采用三維異質(zhì)異構(gòu)集成技術(shù),可將不同工藝、材料甚至生產(chǎn)廠家的芯片或功能模塊立體集成在同一封裝內(nèi),實現(xiàn)產(chǎn)品小型化、高集成和多功能的目標(biāo)。其中,常用的高密度封裝基板主要有硅基板、陶瓷基板以及樹脂基板等。
3.2.1 硅基
硅基射頻微系統(tǒng)在三維集成時通常采用硅通孔TSV(ThroughSiliconVia)、再布線RDL(RedistributionLayer)等工藝技術(shù)實現(xiàn)多層硅片垂直互連,并且采用硅刻蝕技術(shù)將芯片內(nèi)埋入基板內(nèi)達(dá)到進(jìn)一步縮減體積的目的。
3.2.1.1 TSV技術(shù)及硅刻蝕技術(shù)TSV技術(shù)是2.5D/3D集成的關(guān)鍵技術(shù),TSV硅基板表面互連線以及內(nèi)部硅通孔可實現(xiàn)三維異質(zhì)異構(gòu)集成、縮短元器件間距,進(jìn)而提高電路集成密度,實現(xiàn)射頻微系統(tǒng)的小型化和低功耗。TSV技術(shù)大概思路是在硅晶圓上刻蝕出通孔后,向孔內(nèi)填充銅等導(dǎo)體材料,以建立硅片上下表面信號互連通道。其工藝主要實現(xiàn)步驟包括:通孔刻蝕、絕緣層鋪墊(防止產(chǎn)生漏電流,材料通常為SiO2)、通孔填充、圓片減薄以及晶片堆疊與鍵合[13]。
硅刻蝕技術(shù)可依據(jù)要嵌入的芯片厚度并采用干法刻蝕工藝或濕法刻蝕工藝在硅基板上刻蝕出不同深度的空腔,從而將芯片埋入硅基板內(nèi)部,減薄厚度,進(jìn)而提高系統(tǒng)集成度。目前,已有不同深度空腔的一次性刻蝕工藝,即先用濕法刻蝕工藝做出深腔的開窗,然后用干法刻蝕一次性將深腔和淺腔刻出,工藝流程簡單。結(jié)構(gòu)如圖5所示。
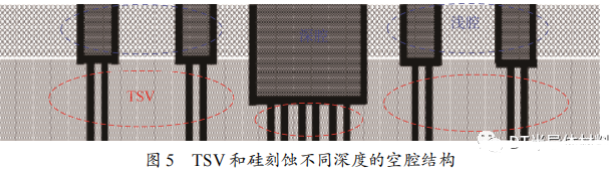
3.2.1.2RDL互連技術(shù)再布線RDL技術(shù)是通過晶圓級金屬布線制程和凸塊制程改變原設(shè)計的芯片線路接點,使集成芯片適用于不同的封裝形式。硅基板RDL大致流程為:先在硅基板上涂覆絕緣層,曝光顯影再電鍍新的金屬導(dǎo)線路徑以連接原有接點和新的凸塊,進(jìn)而重新分布接點,實現(xiàn)高密度、高精度布線要求。工藝通常有兩種:大馬士革工藝和聚合物RDL工藝。如圖6所示,內(nèi)埋芯片可用RDL互連線引出信號到基板表面,結(jié)合FAN-OUT扇出工藝,能有效應(yīng)對引腳較多的芯片。同時,RDL優(yōu)勢還包括:互連線高度較低,上蓋板不需要刻蝕深腔;相對于引線鍵合,其可承受更持久的高溫和更高強(qiáng)度的振動沖擊,增加了元件的可靠性且能取代部分系統(tǒng)設(shè)計,減少設(shè)計時間等。
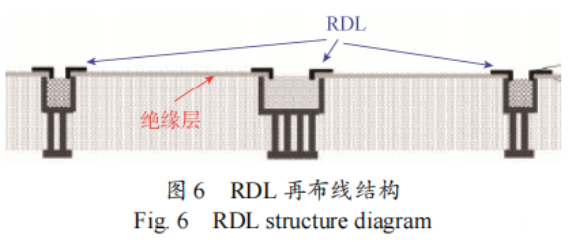
3.2.1.3 微凸點技術(shù)硅基射頻微系統(tǒng)在進(jìn)行三維疊層時,常用技術(shù)主要有微凸點技術(shù)、高分子粘接、Au-Sn共晶焊接等[14],其中微凸點互連技術(shù)采用合金焊料和金屬,電氣互連和散熱性較好,并且具有較為穩(wěn)定的結(jié)構(gòu)支撐性,易于實現(xiàn)高可靠性互連,因而應(yīng)用范圍較廣[15]。微凸點技術(shù)由IBM公司在20世紀(jì)70年代提出,由于其優(yōu)良特性,直到今天仍備受微系統(tǒng)封裝設(shè)計人員的青睞。目前,微凸點的制備方法主要有電沉積法、焊料濺射法、模板印刷焊料法等。其中,電沉積法制作凸點流程[16]如圖7所示。

3.2.1.4 異構(gòu)集成芯粒技術(shù)異構(gòu)集成芯粒(chiplet)技術(shù)起源于多芯片模塊,由AMD公司在上世紀(jì)70年代為降低半導(dǎo)體芯片的設(shè)計成本而提出。芯粒是可以集成到低延遲中介層上的裸片,不同的裸片可以使用不同的工藝節(jié)點制造,甚至可由不同的供應(yīng)商提供。芯粒設(shè)計類似于SoC但價格低于完全集成的SoC設(shè)備,其突破了傳統(tǒng)的在單個硅片上實現(xiàn)所有功能的限制,采用模塊化方法,通過多個被單獨制造的不同功能的芯粒來構(gòu)建硅系統(tǒng),從而減少設(shè)計時間和成本[17]。2017年8月,DARPA啟動通用異構(gòu)集成和IP復(fù)用策略(CHIPS)項目,通過添加較小的專用芯粒來設(shè)計射頻微系統(tǒng)。CHIPS項目的創(chuàng)新之處在于不使用傳統(tǒng)印刷電路板而是用硅中介層(interposer)來連接芯粒,芯粒間通過die-to-die技術(shù)進(jìn)行內(nèi)部互聯(lián),從而實現(xiàn)間距更精細(xì)的互連集成。
3.2.1.5其他技術(shù)Co-EMIB技術(shù)是英特爾在公司已有的嵌入式多核心互連橋接EMIB(Embedded Multi-DieInterconnect Bridge)和FOVEROS基礎(chǔ)上的進(jìn)一步創(chuàng)新,在2019年7月的SEMICONWest會議上被提出。其結(jié)合了EMIB和FOVEROS3D封裝技術(shù)的優(yōu)勢,將多個FOVEROS元件互連為一整個封裝,可以實現(xiàn)其高I/O密度、高帶寬、低功耗、多功能集成。
除以上舉例的幾種硅基射頻微系統(tǒng)異質(zhì)異構(gòu)集成技術(shù)外,還有許多先進(jìn)技術(shù),如臺積電將小外形集成電路封裝SoIC(Systemon Integrated Chips)、集成扇出型封裝InFO(Integrated Fan Out)、晶圓級封裝CoWoS(Chip-on-Wafer-on-Substrate)等3DIC平臺整合在一起推出的3D Fabric先進(jìn)封裝技術(shù);歐洲e-CUBES項目[18]基于TSV技術(shù)和空心通孔及金釘凸點鍵合技術(shù),通過晶圓級封裝可實現(xiàn)嵌入式器件的芯片堆疊3D-WLP(Wafer Level Packaging)和器件級別的三維射頻微系統(tǒng)3DSoC、可壓縮微互連CMIs技術(shù)[19]等等。更多先進(jìn)異質(zhì)異構(gòu)集成技術(shù)還在不斷地涌現(xiàn)發(fā)展,硅基射頻微系統(tǒng)在未來有著巨大的潛力。
3.2.2 陶瓷基
射頻微系統(tǒng)的陶瓷基板采用共燒陶瓷技術(shù)制備。由于燒結(jié)溫度不同,共燒陶瓷[20]主要分為高溫/低溫共燒陶瓷HTCC/LTCC(High-Temperature Co-fired Ceramic/Low-Temperature Co-fired Ceramic),HTCC多層基板具備更高的機(jī)械強(qiáng)度和散熱系數(shù),化學(xué)性能也更為穩(wěn)定,而LTCC基板一般電性能較好、并且可內(nèi)埋無源元件,但機(jī)械強(qiáng)度和導(dǎo)熱率較低。陶瓷基射頻微系統(tǒng)多采用球柵陣列BGA(Ball Grid Array Package)技術(shù)和疊層封裝技術(shù)實現(xiàn)立體封裝。
3.2.2.1 BGA技術(shù)BGA技術(shù)常用于多引腳小尺寸電子產(chǎn)品的封裝。BGA封裝結(jié)構(gòu)如圖8所示,其可在封裝基板背面以面陣列形式排列的焊球代替?zhèn)鹘y(tǒng)鍵合金絲和連接器,用于與外部電路互連并傳遞射頻信號[20],與傳統(tǒng)表面貼裝SMT(Surface Mounted Technology)封裝相比,具有裝配簡單、成本低,布線難度小、互連距離短、尺寸小、焊球可自動對齊等優(yōu)點。根據(jù)基板材料的不同,可以將BGA封裝分為塑封球柵陣列PBGA(Plastic Ball Grid Array)、載帶自動鍵合球柵陣列TBGA(Tape Ball Grid Array)和陶瓷球柵陣列CBGA(Ceramics Ball Grid Array)。其中,CBGA封裝基板材料一般為共燒陶瓷基板。BGA技術(shù)近年來廣受CPU等高密度、高性能、多引腳IC和射頻微系統(tǒng)封裝設(shè)計者的青睞,如英特爾Pentium大功率高集成度CPU芯片采用了CBGA封裝,并在外殼安裝微型風(fēng)冷裝置,以提高電路性能與可靠性。
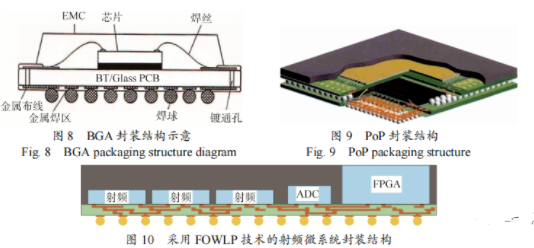
3.2.2.2 PoP技術(shù)疊層封裝PoP(PackageonPackage)技術(shù)在2007年隨iPhone一起進(jìn)入公眾視野。PoP封裝結(jié)構(gòu)如圖9所示[21],其可將先單獨封裝制造的邏輯、存儲和射頻等模塊再垂直堆疊互連集成為一個封裝整體,芯片封裝類型更加靈活,在硅基、陶瓷基、樹脂基的射頻微系統(tǒng)集成中都有應(yīng)用。如2020年6月,在第70屆IEEE電子元件與技術(shù)會議ECTC(ElectronicComponentsandTechnologyConference)上,印度微系統(tǒng)研究人員[22]基于PoP技術(shù)和LTCC工藝設(shè)計了一款用于5G毫米波通信應(yīng)用的收發(fā)射頻微系統(tǒng)封裝,同時,新加坡A*STAR研究所[23]研究人員也對采用扇出型晶圓級封裝FOWLP方法的PoP射頻微系統(tǒng)封裝展示了一些新的研究發(fā)現(xiàn)。
3.2.3 樹脂基
3.2.3.1 FOWLP技術(shù)樹脂基射頻微系統(tǒng)通常采用扇出型晶圓級封裝FOWLP方法,通過晶圓重構(gòu)將多個射頻芯片和數(shù)字芯片粘貼為同一區(qū)域,然后進(jìn)行多層再布線并制備凸點,最后進(jìn)行切割分離,得到能夠與主板射頻互連的一體化微系統(tǒng)封裝[24]。圖10是一種典型的扇出型晶圓級微系統(tǒng)封裝結(jié)構(gòu),相比于傳統(tǒng)的以引線鍵合技術(shù)為基礎(chǔ)的封裝,其在成本、尺寸、性能方面都有突出優(yōu)勢,并可以實現(xiàn)不同功能材料芯片的系統(tǒng)級異質(zhì)異構(gòu)集成。各代工廠都有其獨特的FOWLP方案,如英飛凌的嵌入式晶圓級球柵陣列eWLB(EmbeddedWaferLevelBGA)技術(shù),TSMC的In FOFO WLP技術(shù),三星的FOPLP技術(shù)等。
3.2.3.2 側(cè)邊互聯(lián)技術(shù)
基于樹脂封裝的三維射頻微系統(tǒng),通常先通過層疊的方式對單層微波電路進(jìn)行立體組裝,然后使用樹脂填充封裝,樹脂封裝脫模后對封裝表面金屬化并刻蝕布線,不同層間的射頻垂直互聯(lián)通過采用側(cè)邊互聯(lián)技術(shù)以每層射頻電路端面與側(cè)邊表面類共面波導(dǎo)CPW(Co-PlanarWaveguide)結(jié)構(gòu)的形式實現(xiàn)。圖11展示了一個樹脂包封的三維多芯片射頻組件微系統(tǒng)[25]。
射頻微系統(tǒng)最終目的是要滿足產(chǎn)品微小型化、多功能化、低成本化的發(fā)展趨勢與要求,晶體管技術(shù)、三維異質(zhì)異構(gòu)集成技術(shù)正是服務(wù)于這一目的而誕生和發(fā)展的。先進(jìn)的集成工藝技術(shù)帶來可以滿足民用領(lǐng)域和軍事領(lǐng)域應(yīng)用需求的優(yōu)異產(chǎn)品,而科技進(jìn)步帶來的對微系統(tǒng)集成度和性能更高的要求也在推動著射頻微系統(tǒng)集成技術(shù)的不斷進(jìn)步,繼而攀向一個又一個高峰。
4 射頻微系統(tǒng)熱管理技術(shù)
“小”是電子產(chǎn)品永恒的追求。隨著微系統(tǒng)集成度和小型化程度的不斷提高,微系統(tǒng)封裝內(nèi)熱流密度大等問題逐漸變得不容忽視。傳統(tǒng)熱傳導(dǎo)、強(qiáng)迫液冷、風(fēng)冷等熱管理技術(shù)存在著占用空間大、不易集成、散熱效率低等缺點,已經(jīng)難以滿足高集成度射頻微系統(tǒng)的散熱需求,在保證封裝結(jié)構(gòu)緊湊的前提下如何進(jìn)行高效散熱已成為國內(nèi)外團(tuán)隊的研究重點之一[26,27],現(xiàn)階段射頻微系統(tǒng)常用的熱管理技術(shù)有使用高導(dǎo)熱材料襯底和封裝以及微流道技術(shù)等。
4.1高導(dǎo)熱材料襯底及封裝基于高導(dǎo)熱材料襯底及封裝進(jìn)行散熱的方式設(shè)計簡單可靠,但對材料的熱導(dǎo)率以及與硅、砷化鎵等材料的熱匹配性等性能要求較高,目前較為常用的高熱導(dǎo)率襯底有多層石墨烯、金剛石、碳化硅等,高熱導(dǎo)率熱沉及封裝材料有金剛石基(銅、鋁、銀)、石墨復(fù)合材料等。
DARPA于2011年啟動近結(jié)熱傳輸NJTT(Near-JunctionThermalTransfer)項目[28],目的是通過功率器件的局部熱管理,降低半導(dǎo)體器件熱阻抗,其中一項重要內(nèi)容即為高導(dǎo)熱金剛石襯底。多個研究團(tuán)隊參與研究并取得了一定進(jìn)展[29],如雷神公司采用金剛石襯底實現(xiàn)了GaN器件1/5至1/3的熱阻降低;BAE系統(tǒng)公司將金剛石與薄GaN鍵合以減小熱膨脹系數(shù)CTE(Coefficient of Thermal Expansion)不匹配影響;諾格公司在碳化硅襯底上刻蝕金剛石過孔提高了芯片散熱效果。這方面國內(nèi)起步較晚,目前,中電55所已完成了76.2mm多晶金剛石襯底GaNHEMT的轉(zhuǎn)移鍵合[30]。
國外對高熱導(dǎo)率封裝材料與熱沉研究較早并較為成熟,如金剛石、石墨復(fù)合材料已經(jīng)廣泛用于微電子封裝熱沉。美國勞倫斯利弗莫爾國家實驗室在1995年就開發(fā)出了一種熱導(dǎo)率可達(dá)600W/(m·K)、CTE與硅相近的金剛石-銅復(fù)合材料,并已應(yīng)用于多芯片模塊的熱管理設(shè)計;國內(nèi)北京研究總院和北科大[31]在2009年制備的金剛石-銅復(fù)合材料的熱導(dǎo)率可達(dá)503W/(m·K)。石墨復(fù)合材料的代表性散熱產(chǎn)品有美國愛美達(dá)公司的K-core、珉泰克公司的PYROID熱解石墨等。
4.2微流道技術(shù)微流道技術(shù)由斯坦福大學(xué)的Tuckerman和Pease在1981年提出,并隨著微系統(tǒng)加工工藝的發(fā)展而逐漸成熟。相比于傳統(tǒng)散熱方式,微流道技術(shù)可將散熱性能提升幾個量級,并且更加易于集成、占用體積更小。2006年,IBM公司在風(fēng)冷基礎(chǔ)上開發(fā)出高熱導(dǎo)界面技術(shù),通過制作的芯片表面樹狀結(jié)構(gòu)將散熱效率提升數(shù)倍;之后,蘇黎世實驗室提出噴射沖擊冷卻后再通過樹狀結(jié)構(gòu)迅速回收液體的水冷散熱方案,將散熱效率提升至原先的6倍左右[32];2007年,上海交通大學(xué)聯(lián)合國家重點研究室設(shè)計出了一種新型變截面微流道散熱器,可輸送5×107W/m2的熱通量[33];2012年,DARPA啟動芯片內(nèi)/芯片間增強(qiáng)冷卻ICECool(Inter-Chip Enhancement Cool)項目[34],目標(biāo)是探索先進(jìn)的熱管理技術(shù),其中,嵌入蒸發(fā)微流道冷卻技術(shù)被最為看好以解決遠(yuǎn)端冷卻局限;2017年,普渡大學(xué)在芯片間設(shè)置分級微孔集分水腔和高長寬比微流道陣列等,微流道散熱效率提升10倍;2018年,歐洲微電子研究中心IMEC(Interuniversity Microelectronics Centre)展示了其3D打印的微流道芯片換熱器,可將熱流密度達(dá)100W/cm2的芯片溫升控制在15℃以下。
4.3 其他技術(shù)除上述技術(shù)外,射頻微系統(tǒng)熱管理技術(shù)還在不斷推陳出新。如2015年Kim等[35]人采用熱電薄膜制冷技術(shù)設(shè)計了一種新型散熱器;2018年,中電26所提出了一種基于微冷控制元件的主動微系統(tǒng)冷卻技術(shù)[28],可通過壓電驅(qū)動為內(nèi)部微流道液冷循環(huán)提供足夠的壓力與工作流量,進(jìn)而有效散熱。
5 射頻微系統(tǒng)檢測和測試驗證技術(shù)
射頻微系統(tǒng)檢測和測試驗證主要包括以下內(nèi)容:
?、傥⒅圃旃に嚨臋z測,如TSV結(jié)構(gòu)的漏電流測試、微納結(jié)構(gòu)的擊穿電壓測試、微凸點形貌測試等微缺陷檢測排查;②射頻微系統(tǒng)的電學(xué)性能檢測,如頻率、發(fā)射功率、接收/發(fā)射增益、噪聲等參數(shù)的目標(biāo)符合性驗證;③射頻微系統(tǒng)的可靠性驗證,如TSV/TGV轉(zhuǎn)接板、晶圓鍵合、材料外延的評估,射頻微系統(tǒng)模塊力學(xué)、熱學(xué)可靠性測試與壽命預(yù)測等。
目前,國內(nèi)外多家機(jī)構(gòu)在射頻微系統(tǒng)測試技術(shù)方面都開展了一定研究。日本ASET在2008到2012的5年間,發(fā)展了關(guān)于設(shè)計環(huán)境、芯片測試等技術(shù),以支持日本夢芯工程項目;我國臺灣地區(qū)先進(jìn)堆疊系統(tǒng)與應(yīng)用研發(fā)聯(lián)盟Ad-STAC,整合各種3DIC設(shè)計、技術(shù)、設(shè)備、材料、封裝與測試開展研究,以達(dá)到推動臺灣3DIC設(shè)備及材料自產(chǎn)化的目的[36];長電科技、通富微電、天水華天等企業(yè)均對系統(tǒng)級封裝測試方向進(jìn)行了多年研發(fā),在模型電參數(shù)提取等方面已積累了一定經(jīng)驗;在我國“02”專項、“973”計劃等的支持下,中科院微電子所與多家研究機(jī)構(gòu)聯(lián)合,對射頻微系統(tǒng)三維封裝設(shè)計、TSV測試方法、混合信號芯片測試技術(shù)等關(guān)鍵技術(shù)開展了多項研究并獲得了一定成果[37,38]。
6 射頻微系統(tǒng)發(fā)展策略分析
國外的射頻微系統(tǒng)技術(shù)起步較早,美國、歐洲、日本等發(fā)達(dá)國家早在上世紀(jì)末已將微系統(tǒng)技術(shù)列為先進(jìn)核心技術(shù),近十年來已通過多個工程項目落地了射頻微系統(tǒng)在設(shè)計仿真、三維集成、散熱、封裝測試等方面的各項技術(shù)開發(fā)和應(yīng)用成果。目前,各機(jī)構(gòu)仍然在持續(xù)探索射頻微系統(tǒng)的新材料、新工藝、新技術(shù)。
6.1我國射頻微系統(tǒng)技術(shù)發(fā)展現(xiàn)狀近年來,我國對射頻微系統(tǒng)技術(shù)高度重視。2011年3月,我國完全自主研發(fā)的數(shù)字處理器芯片“魂芯一號”問世,打破了國外高端數(shù)字處理芯片對我國的壟斷;2012年,航天科技集團(tuán)公司元器件保證研究中心組織系統(tǒng)開展了航天未來片上集成系統(tǒng)論證工作,為航天微系統(tǒng)的發(fā)展發(fā)揮了重要作用;2014年,國務(wù)院頒布的《國家集成電路產(chǎn)業(yè)發(fā)展推進(jìn)綱要》中明確指出,到2015年要達(dá)到中國廠商占30%左右先進(jìn)封裝收入的目標(biāo);國發(fā)(2015)28號《中國制造2025》與國發(fā)(2016)43號《“十三五”國家科技創(chuàng)新規(guī)劃》將微系統(tǒng)技術(shù)作為提升新一代信息技術(shù)產(chǎn)業(yè)自主發(fā)展的重要能力,與新一代信息技術(shù)重點進(jìn)行發(fā)展。目前,我國在需求牽引和技術(shù)推動下,已先后支持了機(jī)載綜合處理、遙感信息處理、彈載多模通信等方向的軍用微系統(tǒng)集成課題研究工作,并取得一定成果和進(jìn)展,已初步建成了SoC、SiP微系統(tǒng)技術(shù)平臺和共享IP庫,目標(biāo)是統(tǒng)籌國內(nèi)研究力量打造微系統(tǒng)協(xié)同設(shè)計生態(tài)。
現(xiàn)階段我國與國外射頻微系統(tǒng)發(fā)展存在的差距主要有以下幾點:
?、偕漕l微系統(tǒng)架構(gòu)設(shè)計缺乏深入研究,各領(lǐng)域均缺乏統(tǒng)一的微系統(tǒng)體系評價標(biāo)準(zhǔn)。目前我國射頻微系統(tǒng)成果往往以各個高校、研究所獨立研發(fā)為主,缺乏統(tǒng)一組織、協(xié)同研究的成熟微系統(tǒng)設(shè)計架構(gòu)與研發(fā)路線,對微系統(tǒng)產(chǎn)品許多方面的評價要求與方法尚無統(tǒng)一標(biāo)準(zhǔn),容易出現(xiàn)研究功能重復(fù)、性能相近等問題;另外,對產(chǎn)品的檢測和評價多方溝通流程復(fù)雜,且可能出現(xiàn)指標(biāo)要求大大高于應(yīng)用需求的指標(biāo)浪費的情況。因此,有必要對射頻微系統(tǒng)產(chǎn)品的架構(gòu)設(shè)計進(jìn)行深入研究,并規(guī)范射頻微系統(tǒng)體系評價標(biāo)準(zhǔn),建立規(guī)范化、通用化射頻微系統(tǒng)技術(shù)平臺。
②射頻微系統(tǒng)核心元器件難以滿足航天與武器型號任務(wù)以及民用領(lǐng)域應(yīng)用,仍普遍存在核心芯片依賴進(jìn)口的情況。在當(dāng)前復(fù)雜的國際環(huán)境下,核心技術(shù)受制于人不僅會導(dǎo)致產(chǎn)品生產(chǎn)成本高,并且給武器的供貨保障帶來不穩(wěn)定性;另一方面,可能存在的“芯片后門”也威脅著軍品的安全性,使國防安全存在隱患。因此,迫切需要通過開展國內(nèi)軍用射頻微系統(tǒng)設(shè)計研究,重點掌握相關(guān)集成技術(shù),突破關(guān)鍵封裝工藝瓶頸,打破芯片外部技術(shù)封鎖,實現(xiàn)核心射頻微系統(tǒng)器件的高可靠自主可控。
?、凵漕l微系統(tǒng)多物理場協(xié)同設(shè)計研究不足,技術(shù)攻關(guān)矛盾點較多。一方面,由于射頻微系統(tǒng)通常尺寸較小、集成度高,因此往往功率密度較大、對散熱性能要求較高;另一方面,不同的材料優(yōu)勢側(cè)重點不同,往往很難平衡兼顧產(chǎn)品多種可靠性和電氣性能,在技術(shù)上需要解決較多矛盾點。這就需要研究人員開展微納尺度下的多物理場協(xié)同分析和設(shè)計,考慮多維度物理場下電磁場糾纏效應(yīng)與趨膚效應(yīng)、信號串?dāng)_、熱–力–電耦合匹配等問題,提高產(chǎn)品整體性能。
6.2 我國射頻微系統(tǒng)技術(shù)發(fā)展思考
結(jié)合國內(nèi)射頻微系統(tǒng)發(fā)展現(xiàn)狀,對未來射頻微系統(tǒng)技術(shù)發(fā)展思路提出了以下幾點建議:
?、賹ι漕l微系統(tǒng)進(jìn)行系統(tǒng)需求與架構(gòu)的深入論證,制定規(guī)范統(tǒng)一的射頻微系統(tǒng)研發(fā)流程與評價標(biāo)準(zhǔn),充分整合利用國內(nèi)資源,形成以各大高校、工業(yè)部門研究機(jī)構(gòu)以及軍民企業(yè)為核心的射頻微系統(tǒng)協(xié)同研發(fā)隊伍,建立微系統(tǒng)異構(gòu)集成支撐平臺,發(fā)展協(xié)同創(chuàng)新、合力突破的微系統(tǒng)設(shè)計生態(tài)。
?、趦?yōu)先發(fā)展國家最迫切需求的并能較快取得階段性成果的射頻微系統(tǒng)相關(guān)技術(shù);重點攻堅突破射頻微系統(tǒng)設(shè)計與多物理場協(xié)同仿真、三維異質(zhì)異構(gòu)集成、熱管理與高可靠設(shè)計、微系統(tǒng)測試驗證技術(shù)等射頻微系統(tǒng)關(guān)鍵技術(shù);鼓勵支持推進(jìn)射頻微系統(tǒng)重要基礎(chǔ)研究和核心技術(shù)自主創(chuàng)新。
③關(guān)注射頻微系統(tǒng)方向核心人才培養(yǎng),不斷為射頻微系統(tǒng)研發(fā)隊伍注入高素質(zhì)的新鮮血液,確保微系統(tǒng)持續(xù)有力地蓬勃發(fā)展。
7 結(jié)束語
射頻微系統(tǒng)技術(shù)符合電子信息裝備微型化、智能化、輕質(zhì)化、多功能化、高性能化的永恒追求和發(fā)展趨勢。從技術(shù)突破到產(chǎn)業(yè)發(fā)展,射頻微系統(tǒng)技術(shù)已成為全球最具關(guān)注度、影響力和市場潛力的先進(jìn)技術(shù)之一,未來必將推動軍事與民用工業(yè)的顛覆性進(jìn)步。為滿足我國航天發(fā)射系列任務(wù)與新一代武器裝備需要,應(yīng)結(jié)合射頻微系統(tǒng)發(fā)展趨勢與系統(tǒng)需求,充分探索和利用微系統(tǒng)現(xiàn)有技術(shù)條件,在國家相關(guān)政策的大力支持下,通過對射頻微系統(tǒng)技術(shù)總體布局、規(guī)范標(biāo)準(zhǔn)、協(xié)同設(shè)計、重點突破,在保障我國射頻微 系統(tǒng)技術(shù)快速穩(wěn)健發(fā)展的同時實現(xiàn)技術(shù)創(chuàng)新。
原文信息與來源:《射頻微系統(tǒng)技術(shù)發(fā)展策略研究》 劉德喜,張曉慶,史磊,劉亞威,游月娟
評論