本文目標:明確SMT工程不良產(chǎn)生的相關原因,提高分析速度與效率,針對不良及時加以處理與改善,并加以預防,保證生產(chǎn)產(chǎn)品品質。
<一>錫膏印刷不良判定與相關原因分析:
錫膏印刷應均勻,錫膏應與焊盤尺寸、形狀相等,并與焊盤對齊,錫膏的最少用量應覆蓋住焊盤的75%以上的面積,過量的錫膏最大覆蓋區(qū)域須小于1.2倍的焊盤面積,禁止與相鄰焊盤接觸。以下為印刷的相關不良判定標準與影響印刷不良的相關因素分析:
-
錫膏印刷不良的問題現(xiàn)象:
2. 影響錫膏印刷不良的原因分析
印刷錫膏在整個生產(chǎn)中引起的質量問題占的比重較大,印刷質量與模板的狀況、錫膏設備的刮刀、操作與清洗有
很大關系,解決這類問題要注意各方面的技術要求,一般來說要想印出高質量的錫膏印刷,必須要有:
1)良好適宜的錫膏。
2)良好合理的模板。
3)良好的設備與刮刀。
4)良好的清洗方法與適當?shù)那逑搭l次。
3.錫膏印刷不良相關原因分析與處理方法:
3.1、坍塌
印刷后,錫膏往焊盤兩邊塌陷。產(chǎn)生的原因可能是:
1) 刮刀壓力太大。
2) 印刷板定位不穩(wěn)定。
3) 錫膏粘度或金屬含量過低。
防止或解決辦法:
調整刮刀壓力;重新固定印刷板;選擇合適粘度的錫膏。
3.2、錫膏厚度超下限或偏下限
產(chǎn)生的可能原因是:
1) 模板厚度不符合要求(太薄)。
2) 刮刀壓力過大。
3) 錫膏流動性太差。
防止或解決辦法:
選擇厚度合適的模板;選擇顆粒度和粘度合適的錫膏;調整刮刀壓力。
3.3、厚度不一致
印刷后,焊盤上錫膏厚度不一致,產(chǎn)生的原因可能是:
1) 模板與印刷板不平行。
2) 錫膏攪拌不均勻,使得粘度不一致。
防止或解決辦法:
調整模板與印刷板的相對位置,印刷前充分攪拌錫膏。
3.4、邊緣和表面有毛刺
產(chǎn)生可能原因是錫膏粘度偏低,模板網(wǎng)孔孔壁粗糙或孔壁粘有錫膏。
防止或解決辦法:
鋼網(wǎng)投產(chǎn)前確認檢查網(wǎng)孔的開孔質量,印刷過程中要注意清洗網(wǎng)板。
3.5、印刷均勻
印刷不完全是指焊盤上部分地方?jīng)]印上錫膏。產(chǎn)生的可能原因是:
1) 網(wǎng)孔孔堵塞或部分錫膏粘在模板底部。
2) 錫膏粘度太小。
1) 錫膏中有較大尺寸的金屬粉末顆粒。
2) 刮刀磨損。
防止或解決辦法:清洗網(wǎng)孔和模板底部,選擇粘度合適的錫膏,并使得錫膏印刷能有效地覆蓋整個印刷區(qū)域,選擇金屬粉末顆粒尺寸與窗孔尺寸相對應的錫膏。
3.6、拉尖
拉尖是指漏印后焊盤上的錫膏呈小山峰狀,產(chǎn)生的可能原因是:
印刷間隙或錫膏粘度太大,或鋼網(wǎng)與線路板脫模(即分離)速度過快。
防止或解決辦法:將印刷間隙調整為零間距或選擇合適粘度的錫膏,減小脫模速度。
3.7、偏位
偏位是指印刷后的錫膏偏離焊盤1/4及以上的距離,產(chǎn)生的可能原因是:
1)線路板定位不良(線路板偏位或定位不牢),印刷時產(chǎn)生偏位;
2)印刷時,線路板定位不平整,線路板與鋼網(wǎng)之間有間隙;
3)鋼網(wǎng)與線路板未對中(半自動印刷機);
4)印刷時,線路板與鋼網(wǎng)間存在一定角度的夾角;
5)鋼網(wǎng)變形;
6)鋼網(wǎng)開孔與線路板存在不同方向的偏移;
防止或解決辦法:
檢查線路板定位治具是否良好,有無松動或移位,定位PIN與線路板是否匹配;確認鋼網(wǎng)與線路板是否完全對中,線路板與鋼網(wǎng)間是否存在夾角的情況,并進行相應的調整;檢查鋼網(wǎng)是否變形,鋼網(wǎng)開孔是否與線路板焊盤存在不同方向的偏位現(xiàn)象,確認為鋼網(wǎng)不良,確認處理。
錫膏使用相關要求:
1) 較為理想的使用環(huán)境溫度為20~27℃,相對濕度為40%~60%RH。
2) 平時不使用時應密封保存在冰箱內(nèi)(0~10℃)。
3) 使用時從冰箱中取出放置,須解凍3小時以上,使其達到室溫。使用前要充分攪拌。
<二>元件貼裝不良相關原因分析與應對
1、貼片機拋料原因分析與處理方法:
所謂拋料就是指貼片機在生產(chǎn)過種中,吸取元件之后未進行貼裝,并將元件拋至拋料盒或其它地方,或者未吸取元件而執(zhí)行以上的一個拋料動作。拋料造成材料的損耗,延長了生產(chǎn)時間,降抵了生產(chǎn)效率,提高了生產(chǎn)成本,為優(yōu)化生產(chǎn)效率,降低成本,必須解決拋料率高的問題。以下為拋料主要原因及對策:
原因1:吸嘴問題,吸嘴變形、堵塞或破損造成氣壓不足,漏氣,造成吸料不良,取料不正,識別不良而拋料。
對策:清潔或更換吸嘴;
原因2:識別系統(tǒng)問題,視覺不良,視覺或雷射鏡頭有灰塵或雜物干擾識別,識別光源選擇不當和強度、灰度不夠,還有可能識別系統(tǒng)本身已壞。
對策:清潔擦拭識別系統(tǒng)表面(反光鏡片),保證反光鏡片干凈無雜物沾污等,調整光源強度、灰度,如故障仍未解決,檢查并確認(影像)識別系統(tǒng)硬件;
原因3:取料位置不良,吸嘴在吸取元件時不在元件的中心位置,取料高度不正確(一般以碰到零件后下壓0.05mm為準)而造成取料有偏移,識別時超出規(guī)定的允許誤差而拋料。
對策:使用相機檢查并確認取料位置,必要時調整取料位置;
原因4:真空問題,氣壓不足,真空氣管通道不順暢,有導物堵塞真空通道,或真空有泄漏造成氣壓不足,在對元件吸取時因吸取力度不夠,元件未被吸上或元件被吸取后在貼裝前途中掉落。
對策:檢查貼裝頭各吸嘴對應的電磁閥真空值是否正常,清潔氣路管道;
原因5:程序問題,所運行的貼裝程序中元件參數(shù)設置不當,與來料實物尺寸,亮度等參數(shù)不符造成識別不良而拋料。
對策:修改元件參數(shù),搜尋元件最佳參數(shù)設定;
原因6:來料的問題,來料不規(guī)則,元件引腳氧化等不合格產(chǎn)品。
對策:聯(lián)絡IQC,并將元件不良情況反饋至供應商進行改善;
原因7:供料器問題,供料器位置變形,供料器進料不良(供料器棘齒輪損壞,料帶孔未卡在供料器的棘齒輪上,供料器下方有異物,彈簧老化,或電氣不良),造成取料位置不當或取料不良而拋料,或供料器損壞。
對策:供料器調整,清掃供料器平臺,更換已壞部件或供料器;
當出現(xiàn)拋料不良并到現(xiàn)場進行處理時,技術人員應先詢問設備操作員了解相關情況后,再根據(jù)觀察分析直接找到問題所在,這樣更能有效的找出問題,加以解決,同時提高生產(chǎn)效率,不占用過多的機器生產(chǎn)時間。
2、貼片機其它貼裝不良相關原因分析與處理方法:
不良表現(xiàn)形式 |
不 良 原 因 |
排除方法 |
貼裝頭吸嘴 吸不上元件 |
1、吸嘴開裂引起漏氣 2、吸嘴下表面不平或有錫膏等臟物或吸嘴孔內(nèi)被臟物堵塞 3、吸嘴孔徑與元件不匹配 4、元件表面不平整 5、編帶元件表面的塑膠帶太粘或不結實,塑膠帶從邊緣撕裂開 6、供料器偏離供料中心位置 7、震動供料器滑道中器件的引腳變形,卡在滑道中(管裝元件—振臺) 8、由于編帶供料器卷帶輪松動,送料時塑料帶沒有被卷繞 9、編帶供料器卷帶輪過緊,送料時塑料帶被拉斷 |
更換吸嘴 用細針將吸嘴通孔清洗干凈
更換吸嘴 更換合格元件 重新安裝供料器或更換元件
修改貼裝頭吸料位置 取出滑道中變形的元件
調整編料帶供料器卷帶輪的松緊度
調整編料帶供料器卷帶輪的松緊度
|
貼裝頭吸嘴吸上元件后在貼裝中途丟失元器件 |
1、頭吸嘴的氣路有漏氣現(xiàn)象 2、貼裝頭Z軸不靈活 |
檢查并修復氣路 檢查并保養(yǎng)Z軸 |
貼裝時元件破損 |
1、貼裝頭高度不合適
2、貼裝壓力過大 |
貼裝頭高度要隨PCB厚度和貼裝的元器件高度來調整 重新調整貼裝壓力 |
帶式供料器頂端底部被紙帶或塑料帶堵塞 |
1、 剪帶機不工作或剪刀磨損,使紙帶不能正常排出 2、帶式供料器裝配不當或步進齒輪損壞 |
檢查并修復剪帶機 更換或重新裝配供料器 |
貼裝偏位 |
1、個別元器件的貼裝坐標不準確 2、編程后或貼片一段時間后整個PCB上的元器件位置有少量偏移 |
修改個別位置的貼裝坐標 可用OFSET修正X、Y、θ值
|
元器件貼裝 方向錯 |
1、貼片編程錯誤 2、供料器裝料錯誤 3、元器件生產(chǎn)廠家不同,編帶時方向不一致 4、向振臺加料時將管裝料方向上錯 |
修改貼片程序 確認裝料方向并重新裝料 更換編帶元器件時注意方向 加料時注意元器件的方向 |
貼裝頭在吸取元件時吸嘴損壞 |
1、供料器未裝配到位
2、貼裝高度不當,偏下限 |
確認供料器是否裝配良好,并重新裝配 修改Z軸高度 |
<三>回流焊接不良相關原因分析與應對:
序號 |
主要缺陷 |
原 因 |
解決方法 |
1 |
焊錫球 (錫珠) |
焊膏不良—已氧化 焊膏有水分 焊膏過多 加熱速度過快 元件放置壓力過大 |
增強活性 降低周圍環(huán)境濕度 減小網(wǎng)板開孔,增大刮刀壓力 調整溫度—時間曲線 減小壓力 |
2 |
連 焊 (短路) |
焊膏塌落 網(wǎng)板背面有焊膏 加熱速度過快 焊膏過多 網(wǎng)板質量不好 |
增加焊膏金屬含量或粘度 降低刮刀壓力,采用接觸式印刷 調整溫度—時間曲線 減小網(wǎng)板開孔,增大刮刀壓力 采用激光切割模板 |
3 |
元件豎立 (浮起) |
加熱速度過快及不均勻 元件可焊性差 |
調整溫度—時間曲線 選用可焊性好的焊膏 |
4 |
焊錫過多 (多錫) |
網(wǎng)板開孔過大 焊膏粘度小 網(wǎng)板太厚 |
減小網(wǎng)板開孔 檢查焊膏粘度 減小網(wǎng)板厚度 |
5 |
焊錫不足 (少錫) |
網(wǎng)板質量差 焊膏不夠
模板與印制板虛位 回流時間短 刮刀速度快,網(wǎng)板太厚 |
采用激光切割模板 增加網(wǎng)板開孔,降低壓力 用金屬刮刀 采用接觸式印刷 加長回流時間 降低刮刀速度,減小網(wǎng)板厚度 |
序號 |
主要缺陷 |
原 因 |
解決方法 |
6 |
錫膏塌落 |
錫膏粘度低 環(huán)境溫度高 |
選擇合適錫膏 控制環(huán)境溫度 |
7 |
虛 焊 |
印刷參數(shù)不正確,引起錫膏不足 錫膏升過元件引腳 焊盤有阻焊膜及污物 |
減小錫膏粘度,檢查刮刀壓力 調整溫度—時間曲線 檢查網(wǎng)板(鋼網(wǎng)) |
錫珠產(chǎn)生原因分析
一般來說,錫珠的產(chǎn)生原因是多方面,綜合的。錫膏的印刷厚度、錫膏的組成及氧化度、模板的制作及開口、錫膏是否吸收了水分、元件貼裝壓力、元器件及焊盤的可焊性、再流焊溫度的設置、外界環(huán)境的影響都可能是焊錫珠產(chǎn)生的原因。錫珠的直徑大致在0.2mm~0.4mm之間,也有超過此范圍的,主要集中在片式阻容元件的周圍。焊錫珠的存在,不僅影響了電子產(chǎn)品的外觀,也對產(chǎn)品的質量埋下了隱患。原因是現(xiàn)代化印制板元件密度高,間距小,焊錫珠在使用時可能脫落,從而造成元件短路,影響電子產(chǎn)品的質量。
1、錫膏的金屬含量。錫膏中金屬含量其質量比約為88%~92%,體積比約為50%。當金屬含量增加時,錫膏的黏度
增加,就能有效地抵抗預熱過程中汽化產(chǎn)生的力。另外,金屬含量的增加,使金屬粉末排列緊密,使其在熔化時更容結合而不被吹散。此外,金屬含量的增加也可能減小錫膏印刷后的“塌落”,因此,不易產(chǎn)生焊錫珠。
2、錫膏的金屬氧化度。在錫膏中,金屬氧化度越高在焊接時金屬粉末結合阻力越大,錫膏與焊盤及元件之間就越不
浸潤,從而導致可焊性降低。實驗表明:焊錫珠的發(fā)生率與金屬粉末的氧化度成正比。一般的,錫膏中的焊料氧化度應控制在0.05%以下,最大極限為0.15%。
3、錫膏中金屬粉末的粒度。錫膏中粉末的粒度越小,錫膏的總體表面積就越大,從而導致較細粉末的氧化度較高,
因而焊錫珠現(xiàn)象加劇。我們的實驗表明:選用較細顆粒度的錫膏時,更容易產(chǎn)生焊錫粉。
4、錫膏在印制板上的印刷厚度。錫膏印刷后的厚度是印刷的一個重要參數(shù),通常在120~200um之間。錫膏過厚會造成錫膏的“塌落”,促進焊錫珠的產(chǎn)生。
5、錫膏中助焊劑的量及焊劑的活性。焊劑量太多,會造成錫膏的局部塌落,從而使焊錫珠容易產(chǎn)生。另外,焊劑的活性小時,焊劑的去氧化能力弱,從而也容易產(chǎn)生錫珠。免清洗錫膏的活性較松香型和水溶型錫膏要低,因此就更有可能產(chǎn)生焊錫珠。
6、此外,錫膏在使用前,須進行3小時以上的解凍,否則,錫膏容易吸收水分,在回流焊接時焊錫飛濺而產(chǎn)生錫珠。
7、鋼網(wǎng)開孔
合適的模板開孔形狀及尺寸也會減少焊錫球的產(chǎn)生。
8.印制不良線路板的清洗
對印制不良線路板進行清洗時,若未清洗干凈,印制板表面和過孔內(nèi)就會殘余的部分錫膏,焊接時就會形成錫珠。因此須加強操作員在生產(chǎn)過程中的責任心,與線路板的清洗方法,嚴格按照工藝要求進行生產(chǎn),加強工藝過程的質量控制。
9、元件貼裝壓力及元器件的可焊性。
如果元件在貼裝時壓力過大,錫膏就容易被擠壓到元件下面的阻焊層上,在再流焊時焊錫熔化跑到元件的周圍形成焊錫珠。
解決方法:
減小貼裝時的壓力,并采用上面推薦使用的模板開口形式,避免錫膏被擠壓到焊盤外邊去。另外,元件和焊盤焊性也有直接影響,如果元件和焊盤的氧化度嚴重,也會造成焊錫珠的產(chǎn)生。經(jīng)過熱風整平的焊盤在錫膏印刷后,改變了焊錫與焊劑的比例,使焊劑的比例降低,焊盤越小,比例失調越嚴重,這也是產(chǎn)生焊錫珠的一個原因。
綜上可見,焊錫珠的產(chǎn)生是一個極復雜的過程,我們在調整參數(shù)時應綜合考慮,在生產(chǎn)中摸索經(jīng)驗,達到對焊錫珠的最佳控制。
無鉛系列溫度曲線基準:
根據(jù)現(xiàn)有焊接設備,結合現(xiàn)在使用焊膏的規(guī)格參數(shù),結合產(chǎn)品實際的生產(chǎn)焊接情況制定出較為理想的溫度曲線圖(無鉛系列):
1、熱風回流焊接時間與溫度的關系
第一階段為升溫階段,在這一階段印制板從室溫上升到150℃,持續(xù)時間為75秒左右,主要目的是使焊膏中
的溶劑揮發(fā),升溫速度不可太快,一般控制在4℃/S以內(nèi)。
第二階段為預熱保溫階段,其目的是除去過剩的溶劑及水分,以防止印制板因急劇升溫帶來的熱應力,促使
助焊劑和化。預熱溫度控制在150-200℃,預熱時間控制在60~180秒范圍內(nèi)。錫膏開始熔化,潤濕焊點
部位。在該階段需注意:既要使印制板和元器件充分預熱,減少熱沖擊,又要避免過熱,使助焊劑提前失效,造
成板材、元器件損壞。
第三階段為焊接階段,220℃以上保持時間控制在25-50秒之間,時間不宜太長,焊接溫度最高240℃以內(nèi)。
第四階段為冷卻階段,宜采用強風冷卻,便于形成細密組織。
產(chǎn)生原因 |
改善對策 |
空焊 |
|
1、錫膏活性較弱; |
1、更換活性較強的錫膏; |
2、鋼網(wǎng)開孔不佳; |
2、開設精確的鋼網(wǎng); |
3、銅鉑間距過大或大銅貼小元件; |
3、將來板不良反饋于供應商或鋼網(wǎng)將焊盤間距開為0.5mm; |
4、刮刀壓力太大; |
4、調整刮刀壓力; |
5、元件腳平整度不佳(翹腳、變形) |
5、將元件使用前作檢視并修整; |
6、回焊爐預熱區(qū)升溫太快; |
6、調整升溫速度90-120秒; |
7、PCB銅鉑太臟或者氧化; |
7、用助焊劑清洗PCB; |
8、PCB板含有水份; |
8、對PCB進行烘烤; |
9、機器貼裝偏移; |
9、調整元件貼裝座標; |
10、錫膏印刷偏移; |
10、調整印刷機; |
11、機器夾板軌道松動造成貼裝偏移; |
11、松掉X、Y Table軌道螺絲進行調整; |
12、MARK點誤照造成元件打偏,導致空焊; |
12、重新校正MARK點或更換MARK點; |
13、PCB銅鉑上有穿孔; |
13、將網(wǎng)孔向相反方向銼大; |
14、機器貼裝高度設置不當; |
14、重新設置機器貼裝高度; |
15、錫膏較薄導致少錫空焊; |
15、在網(wǎng)網(wǎng)下墊膠紙或調整鋼網(wǎng)與PCB間距; |
16、錫膏印刷脫膜不良。 |
16、開精密的激光鋼鋼,調整印刷機; |
17、錫膏使用時間過長,活性劑揮發(fā)掉; |
17、用新錫膏與舊錫膏混合使用; |
18、機器反光板孔過大誤識別造成; |
18、更換合適的反光板; |
19、原材料設計不良; |
19、反饋IQC聯(lián)絡客戶; |
20、料架中心偏移; |
20、校正料架中心; |
21、機器吹氣過大將錫膏吹跑; |
21、將貼片吹氣調整為0.2mm/cm2; |
22、元件氧化; |
22、吏換OK之材料; |
23、PCB貼裝元件過長時間沒過爐,導致活性劑揮發(fā); |
23、及時將PCBA過爐,生產(chǎn)過程中避免堆積; |
24、機器Q1.Q2軸皮帶磨損造成貼裝角度偏信移過爐后空焊; |
24、更換Q1或Q2皮帶并調整松緊度; |
25、流拉過程中板邊元件錫膏被擦掉造成空焊; |
25、將軌道磨掉,或將PCB轉方向生產(chǎn); |
26、鋼網(wǎng)孔堵塞漏刷錫膏造成空焊。 |
26、清洗鋼網(wǎng)并用風槍吹鋼網(wǎng)。 |
短路 |
|
1、鋼網(wǎng)與PCB板間距過大導致錫膏印刷過厚短路; |
1、調整鋼網(wǎng)與PCB間距0.2mm-1mm; |
2、元件貼裝高度設置過低將錫膏擠壓導 致短路; |
2、調整機器貼裝高度,泛用機一般調整到元悠揚與吸咀接觸到為宜(吸咀下將時); |
3、回焊爐升溫過快導致; |
3、調整回流焊升溫速度90-120sec; |
4、元件貼裝偏移導致; |
4、調整機器貼裝座標; |
5、鋼網(wǎng)開孔不佳(厚度過厚,引腳開孔過長,開孔過大); |
5、重開精密鋼網(wǎng),厚度一般為0.12mm-0.15mm; |
6、錫膏無法承受元件重量; |
6、選用粘性好的錫膏; |
7、鋼網(wǎng)或刮刀變形造成錫膏印刷過厚; |
7、更換鋼網(wǎng)或刮刀; |
8、錫膏活性較強; |
8、更換較弱的錫膏; |
9、空貼點位封貼膠紙卷起造成周邊元件錫膏印刷過厚; |
9、重新用粘性較好的膠紙或錫鉑紙貼; |
10、回流焊震動過大或不水平; |
10、調整水平,修量回焊爐; |
11、鋼網(wǎng)底部粘錫; |
11、清洗鋼網(wǎng),加大鋼網(wǎng)清洗頻率; |
12、QFP吸咀晃動貼裝偏移造成短路。 |
12、更換QFP吸咀。 |
直立 |
|
1、銅鉑兩邊大小不一產(chǎn)生拉力不均; |
1、開鋼網(wǎng)時將焊盤兩端開成一樣; |
2、預熱升溫速率太快; |
2、調整預熱升溫速率; |
3、機器貼裝偏移; |
3、調整機器貼裝偏移; |
4、錫膏印刷厚度不均; |
4、調整印刷機; |
5、回焊爐內(nèi)溫度分布不均; |
5、調整回焊爐溫度; |
6、錫膏印刷偏移; |
6、調整印刷機; |
7、機器軌道夾板不緊導致貼裝偏移; |
7、重新調整夾板軌道; |
8、機器頭部晃動; |
8、調整機器頭部; |
9、錫膏活性過強; |
9、更換活性較低的錫膏; |
10、爐溫設置不當; |
10、調整回焊爐溫度; |
11、銅鉑間距過大; |
11、開鋼網(wǎng)時將焊盤內(nèi)切外延; |
12、MARK點誤照造成打偏; |
12、重新識別MARK點或更換MARK點; |
13、料架不良,吸著不穩(wěn)打偏; |
13、更換或維修料架; |
14、原材料不良; |
14、更換OK材料; |
15、鋼網(wǎng)開孔不良; |
15、重新開設精密鋼網(wǎng); |
16、吸咀磨損嚴重; |
16、更換OK吸咀; |
17、機器厚度檢測器誤測。 |
17、修理調整厚度檢測器。 |
缺件 |
|
1、真空泵碳片不良真空不夠造成缺件; |
1、更換真空泵碳片,或真空泵; |
2、吸咀堵塞或吸咀不良; |
2、更換或保養(yǎng)吸膈; |
3、元件厚度檢測不當或檢測器不良; |
3、修改元悠揚厚度誤差或檢修厚度檢測器; |
4、貼裝高度設置不當; |
4、修改機器貼裝高度; |
5、吸咀吹氣過大或不吹氣; |
5、一般設為0.1-0.2kgf/cm2; |
6、吸咀真空設定不當(適用于MPA); |
6、重新設定真空參數(shù),一般設為6以下; |
7、異形元件貼裝速度過快; |
7、調整異形元件貼裝速度; |
8、頭部氣管破烈; |
8、更換頭部氣管; |
9、氣閥密封圈磨損; |
9、保養(yǎng)氣閥并更換密封圈; |
10、回焊爐軌道邊上有異物擦掉板上元件; |
10、打開爐蓋清潔軌道; |
11、頭部上下不順暢; |
11、拆下頭部進行保養(yǎng); |
12、貼裝過程中故障死機丟失步驟; |
12、機器故障的板做重點標示; |
13、軌道松動,支撐PIN高不同; |
13、鎖緊軌道,選用相同的支撐PIN; |
14、錫膏印刷后放置時間過久導致地件無法粘上。 |
14、將印刷好的PCB及時清理下去。 |
錫珠 |
|
1、回流焊預熱不足,升溫過快; |
1、調整回流焊溫度(降低升溫速度); |
2、錫膏經(jīng)冷藏,回溫不完全; |
2、錫膏在使用前必須回溫4H以上; |
3、錫膏吸濕產(chǎn)生噴濺(室內(nèi)濕度太重); |
3、將室內(nèi)溫度控制到30%-60%); |
4、PCB板中水份過多; |
4、將PCB板烘烤; |
5、加過量稀釋劑; |
5、避免在錫膏內(nèi)加稀釋劑; |
6、鋼網(wǎng)開孔設計不當; |
6、重新開設密鋼網(wǎng); |
7、錫粉顆粒不均。 |
7、更換適用的錫膏,按照規(guī)定的時間對錫膏進行攪拌:回溫4H攪拌4M。 |
翹腳 |
|
1、原材料翹腳; |
1、生產(chǎn)前先對材料進行檢查,有NG品修好后再貼裝; |
2、規(guī)正座內(nèi)有異物; |
2、清潔歸正座; |
3、MPA3 chuck不良; |
3、對MPA3 chuck進行維修; |
4、程序設置有誤; |
4、修改程序; |
5、MK規(guī)正器不靈活;。 |
5、拆下規(guī)正器進行調整。 |
高件 |
|
1、PCB 板上有異物; |
1、印刷前清洗干凈; |
2、膠量過多; |
2、調整印刷機或點膠機; |
3、紅膠使用時間過久; |
3、更換新紅膠; |
4、錫膏中有異物; |
4、印刷過程避免異物掉過去; |
5、爐溫設置過高或反面元件過重; |
5、調整爐溫或用紙皮墊著過爐; |
6、機器貼裝高度過高。 |
6、調整貼裝高度。 |
錯件 |
|
1、機器貼裝時無吹氣拋料無吹氣,拋料盒毛刷不良; |
1、檢查機器貼片吹氣氣壓拋料吹氣氣壓拋料盒毛刷; |
2、貼裝高度設置過高元件未貼裝到位; |
2、檢查機器貼裝高度; |
3、頭部氣閥不良; |
3、保養(yǎng)頭部氣閥; |
4、人為擦板造成; |
4、人為擦板須經(jīng)過確認后方可過爐; |
5、程序修改錯誤; |
5、核對程序; |
6、材料上錯; |
6、核對站位表,OK后方可上機; |
7、機器異常導致元件打飛造成錯件。 |
7、檢查引起元件打飛的原因。 |
反向 |
|
1、程序角度設置錯誤; |
1、重新檢查程序; |
2、原材料反向; |
2、上料前對材料方向進行檢驗; |
3、上料員上料方向上反; |
3、上料前對材料方向進行確認; |
4、FEEDER壓蓋變開導致,元件供給時方向; |
4、維修或更換FEEDER壓蓋; |
5、機器歸正件時反向; |
5、修理機器歸正器; |
6、來料方向變更,盤裝方向變更后程序未變更方向; |
6、發(fā)現(xiàn)問題時及時修改程序; |
7、Q、V軸馬達皮帶或軸有問題。 |
7、檢查馬達皮帶和馬達軸。 |
反白 |
|
1、料架壓蓋不良; |
1、維修或更換料架壓蓋; |
2、原材料帶磁性; |
2、更換材料或在料架槽內(nèi)加磁皮; |
3、料架頂針偏位; |
3、調整料架偏心螺絲; |
4、原材料反白; |
4、生產(chǎn)前對材料進行檢驗。 |
冷焊 |
|
1、回焊爐回焊區(qū)溫度不夠或回焊時間不足; |
1、調整回焊爐溫度或鏈條速度; |
2、元件過大氣墊量過大; |
2、調整回焊度回焊區(qū)溫度; |
3、錫膏使用過久,熔劑渾發(fā)過多。 |
3、更換新錫膏。 |
偏移 |
|
1、印刷偏移; |
1、調整印刷機印刷位置; |
2、機器夾板不緊造成貼偏; |
2、調整XYtable軌道高度; |
3、機器貼裝座標偏移; |
3、調整機器貼裝座標; |
4、過爐時鏈條抖動導致偏移; |
4、拆下回焊爐鏈條進行修理; |
5、MARK點誤識別導致打偏; |
5、重新校正MARK點資料 ; |
6、NOZZLE中心偏移,補償值偏移; |
6、校正吸咀中心; |
7、吸咀反白元件誤識別; |
7、更換吸咀; |
8、機器X軸或Y軸絲桿磨損導致貼裝偏移; |
8、更換X軸或Y軸絲桿或套子; |
9、機器頭部滑塊磨損導致貼偏; |
9、更換頭部滑塊; |
10、驅動箱不良或信號線松動; |
10、維修驅動箱或將信號線鎖緊; |
11、783或驅動箱溫度過高; |
11、檢查783或驅動箱風扇; |
12、MPA3吸咀定位鎖磨損導致吸咀晃動造成貼裝偏移。 |
12、更換MAP3吸咀定位鎖。 |
少錫 |
|
1、PCB焊盤上有貫穿孔; |
1、開鋼網(wǎng)時避孔處理; |
2、鋼網(wǎng)開孔過小或鋼網(wǎng)厚度太薄; |
2、開鋼網(wǎng)時按標準開鋼網(wǎng); |
3、錫膏印刷時少錫(脫膜不良); |
3、調整印刷機刮刀壓力和PCB與鋼網(wǎng)間距; |
4、鋼網(wǎng)堵孔導致錫膏漏刷。 |
4、清洗鋼網(wǎng)并用氣槍。 |
損件 |
|
1、原材料不良; |
1、檢查原材料并反饋IQC處理; |
2、規(guī)正器不順導致元件夾壞; |
2、維修調整規(guī)正座; |
3、吸著高度或貼裝高度過低導致; |
3、調整機器貼裝高度; |
4、回焊爐溫度設置過高; |
4、調整回焊爐溫度; |
5、料架頂針過長導致; |
5、調整料架頂針; |
6、爐后撞件。 |
6、人員作業(yè)時注意撞件。 |
多錫 |
|
1、鋼網(wǎng)開孔過大或厚度過厚; |
1、開鋼網(wǎng)時按標準開網(wǎng); |
2、錫膏印刷厚過厚; |
2、調整PCB與鋼網(wǎng)間距; |
3、鋼網(wǎng)底部粘錫; |
3、清洗鋼網(wǎng); |
4、修理員回錫過多 |
4、教導修理員加錫時按標準作業(yè)。 |
打橫 |
|
1、吸咀真空不中; |
1、清洗吸咀或更換過濾棒; |
2、吸咀頭松動; |
2、更換吸咀; |
3、機器⊙軸松動導致; |
3、調整機器⊙軸; |
4、原材料料槽過大; |
4、更換材料; |
5、元件貼裝角度設置錯誤; |
5、修改程序貼裝角度; |
6、真空氣管漏氣。 |
6、更換真空氣閥。 |
金手指粘錫 |
|
1、PCB未清洗干凈; |
1、PCB清洗完后經(jīng)確認后投產(chǎn); |
2、印刷時鋼網(wǎng)底部粘錫導致; |
2、清洗鋼網(wǎng),并用高溫膠紙把金手指封體; |
3、輸送帶上粘錫。 |
3、清洗輸送帶。 |
溢膠 |
|
1、紅膠印刷偏移; |
1、調整印刷機; |
2、機器點膠偏移或膠量過大; |
2、調整點膠機座標及膠量; |
3、機器貼裝偏移; |
3、調整機器貼裝位置; |
4、鋼網(wǎng)開孔不良; |
4、重新按標準開設鋼網(wǎng); |
5、機器貼裝高度過低; |
5、調整機器貼裝高度; |
6、紅膠過稀。 |
6、將紅膠冷凍后再使用。 |
最后補充說的幾句話:
1、出了問題,研發(fā)人員不能直接把問題丟給生產(chǎn),硬件工程師應該具備量產(chǎn)的生產(chǎn)知識,并能夠指導或者協(xié)助生產(chǎn)人員定位和解決問題,優(yōu)化流程。硬件工程師的本質是對硬件產(chǎn)品的全部生命流程負責。不是就把原理圖畫好,PCB拉線拉好就結束了。
2、優(yōu)化鋼網(wǎng)的工作,不只是鋼網(wǎng)生產(chǎn)環(huán)節(jié)的問題。PCB封裝設計時,就需要充分考慮清楚,鋼網(wǎng)開孔的大小。特別是BGA的鋼網(wǎng)開孔尺寸非常影響良率。
3、SMT的問題,往往是來料和PCB的問題,不能只是盯著SMT這個環(huán)節(jié)。需要考慮采購、庫存保管、PCB設計加工等等環(huán)節(jié)可能引入的風險。
審核編輯 :李倩
-
錫膏
+關注
關注
1文章
797瀏覽量
16601 -
焊盤
+關注
關注
6文章
545瀏覽量
38059
原文標題:是否正在為SMT良率苦惱?看看原因與措施!
文章出處:【微信號:Hardware_10W,微信公眾號:硬件十萬個為什么】歡迎添加關注!文章轉載請注明出處。
發(fā)布評論請先 登錄
相關推薦
淺談影響晶圓分選良率的因素(2)
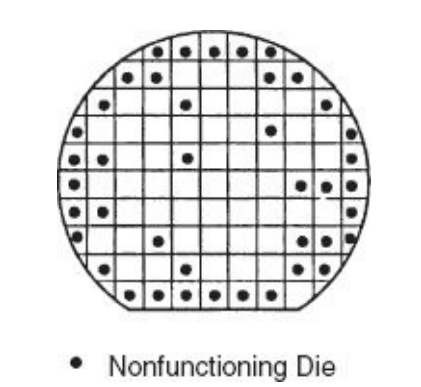
關于SMT貼片生產(chǎn)中導致拋料原因分析
SMT貼片加工產(chǎn)生焊接裂縫的原因是什么?
半導體工藝之生產(chǎn)力和工藝良率
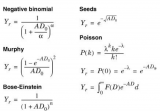
傳三星電子12nm級DRAM內(nèi)存良率不足五成
SMT貼片加工物料損耗的各種因素、原因與相應的解決方法
SMT貼片加工發(fā)生短路的原因及解決方法
OpenAI正在為ChatGPT開發(fā)全新的搜索功能
為什么說“AOI檢測”是SMT焊接質量的把關者?
smt貼片BGA焊點斷裂的原因和對策
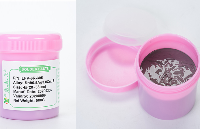
評論